Top 10 Marine Auxiliary Machinery Systems Explained
Discover the top 10 marine auxiliary machinery systems, from pumps to purifiers, and learn how they ensure safe, efficient ship operations.
Marine auxiliary machinery systems are the unsung heroes of maritime operations, powering everything from electricity generation to waste management while supporting the main propulsion engine. These systems ensure safety, efficiency, and environmental compliance on vessels ranging from colossal tankers to modest fishing boats. This comprehensive guide explores the top 10 marine auxiliary machinery systems, their functions, specifications, and critical roles in modern shipping.
Why Marine Auxiliary Machinery Matters
The main engine may propel a ship, but auxiliary machinery keeps it operational. These systems manage critical tasks like fuel purification, power distribution, and sewage treatment, enabling vessels to comply with stringent regulations like those set by the International Maritime Organization (IMO). Failures in auxiliary systems, such as oily water separators or steering gear, can lead to vessel detentions, environmental fines, or even catastrophic incidents. According to classification society DNV, auxiliary machinery issues account for a significant portion of shipboard incidents, emphasizing their importance.
On Unattended Machinery Space (UMS) vessels, where automation reigns, auxiliary systems must operate with near-perfect reliability. Integrated Control and Automation Systems (ICAS) monitor these machines in real-time, reducing human intervention while enhancing efficiency. Let’s dive into the top 10 systems that keep ships moving.
1. Marine Pumps: The Heart of Fluid Management
Marine pumps are indispensable, circulating fluids like fuel, lubricating oil, cooling water, and bilge water. They ensure the main engine operates smoothly, maintain vessel stability through ballasting, and support firefighting efforts.
Types and Applications
Pump Type | Application | Flow Rate (Typical) | Pressure (Typical) |
---|---|---|---|
Centrifugal | Seawater cooling, ballast transfer | 100–5000 m³/h | 1–5 bar |
Reciprocating | Boiler feed, high-pressure fuel | 0.5–50 m³/h | 10–100 bar |
Screw/Gear | Lubricating oil, heavy fuel oil | 1–100 m³/h | 5–20 bar |
Key Features
- Material: Bronze or stainless steel for corrosion resistance in seawater applications.
- Power Source: Electric or hydraulic, depending on the ship’s design.
- IMO Compliance: Pumps handling bilge water must align with MARPOL Annex I to prevent pollution.
Real-World Impact
On tankers, centrifugal pumps transfer thousands of cubic meters of cargo oil per hour, while firefighting pumps deliver high-pressure water to protect crew and vessel during emergencies.
2. Purifiers and Separators: Ensuring Clean Fuel and Oil
Purifiers and separators remove water, sludge, and contaminants from fuel oil (FO), diesel oil (DO), and lubricating oil (LO). Clean fluids are critical for efficient combustion and reduced wear on engine components like injectors and piston rings.
How They Work
Centrifugal purifiers spin fluids at high speeds (up to 10,000 RPM), separating heavier impurities based on density. Modern systems feature:
- Self-Cleaning: Automatic sludge discharge.
- Fuel Oil Monitoring Systems (FOMS): Real-time contamination detection.
- Preheating: Fuel heated to ~98°C for heavy fuel oil (HFO) to optimize separation.
Specifications
Parameter | Typical Value |
---|---|
Throughput | 500–10,000 liters/hour |
Bowl Speed | 6,000–12,000 RPM |
Power Consumption | 5–20 kW |
Best Practice
Match centrifuge operation to fuel viscosity curves, ensuring preheated temperatures align with manufacturer guidelines to avoid engine damage.
3. Air Compressors and Starting Air Systems: Powering Engine Starts
Air compressors supply compressed air for starting main and auxiliary engines, operating pneumatic tools, and powering control systems. Stored in air bottles at ~30 bar, compressed air ensures reliable engine starts and deck operations.
Components
- Main Compressors: Typically reciprocating or screw-type.
- Air Bottles: High-pressure storage tanks.
- Control Air Filters/Dryers: Remove moisture to prevent corrosion.
Challenges
High-humidity ports can cause starting air valve failures, delaying departures. Regular maintenance of filters and dryers mitigates this risk.
Specifications
Component | Specification |
---|---|
Compressor Capacity | 50–500 m³/h |
Air Bottle Pressure | 25–40 bar |
Power Requirement | 10–50 kW |
4. Freshwater Generators: Sustaining Life at Sea
Freshwater generators produce potable water for crew consumption, engine jacket cooling, and boiler feedwater. They use waste heat or reverse osmosis to convert seawater into freshwater.
Types
- Evaporators (Flash Distillers): Utilize waste heat from jacket cooling water or steam.
- Reverse Osmosis (RO) Systems: Filter seawater through semi-permeable membranes.
Advancements
Energy Recovery Devices (ERDs) in RO systems reduce fuel consumption by 30–50%, making them popular on modern vessels.
Specifications
Type | Capacity | Energy Source |
---|---|---|
Evaporator | 1–50 tons/day | Waste heat (60–90°C) |
RO System | 5–100 tons/day | Electric (5–15 kW/ton) |
5. Boilers and Exhaust Gas Economizers: Steam for Operations
Marine boilers generate steam for fuel heating, tank cleaning, and auxiliary machinery like cargo pumps on tankers. Exhaust Gas Economizers (EGEs) recover waste heat from main engine exhaust, improving fuel efficiency.
Safety Regulations
Per SOLAS Chapter II-1, boilers are pressure vessels requiring regular inspections and safety valve testing.
Specifications
System | Steam Output | Fuel Type |
---|---|---|
Auxiliary Boiler | 1–20 tons/hour | MGO, HFO |
EGE | 0.5–10 tons/hour | Exhaust gas (200–400°C) |
Chart: Boiler System Flow
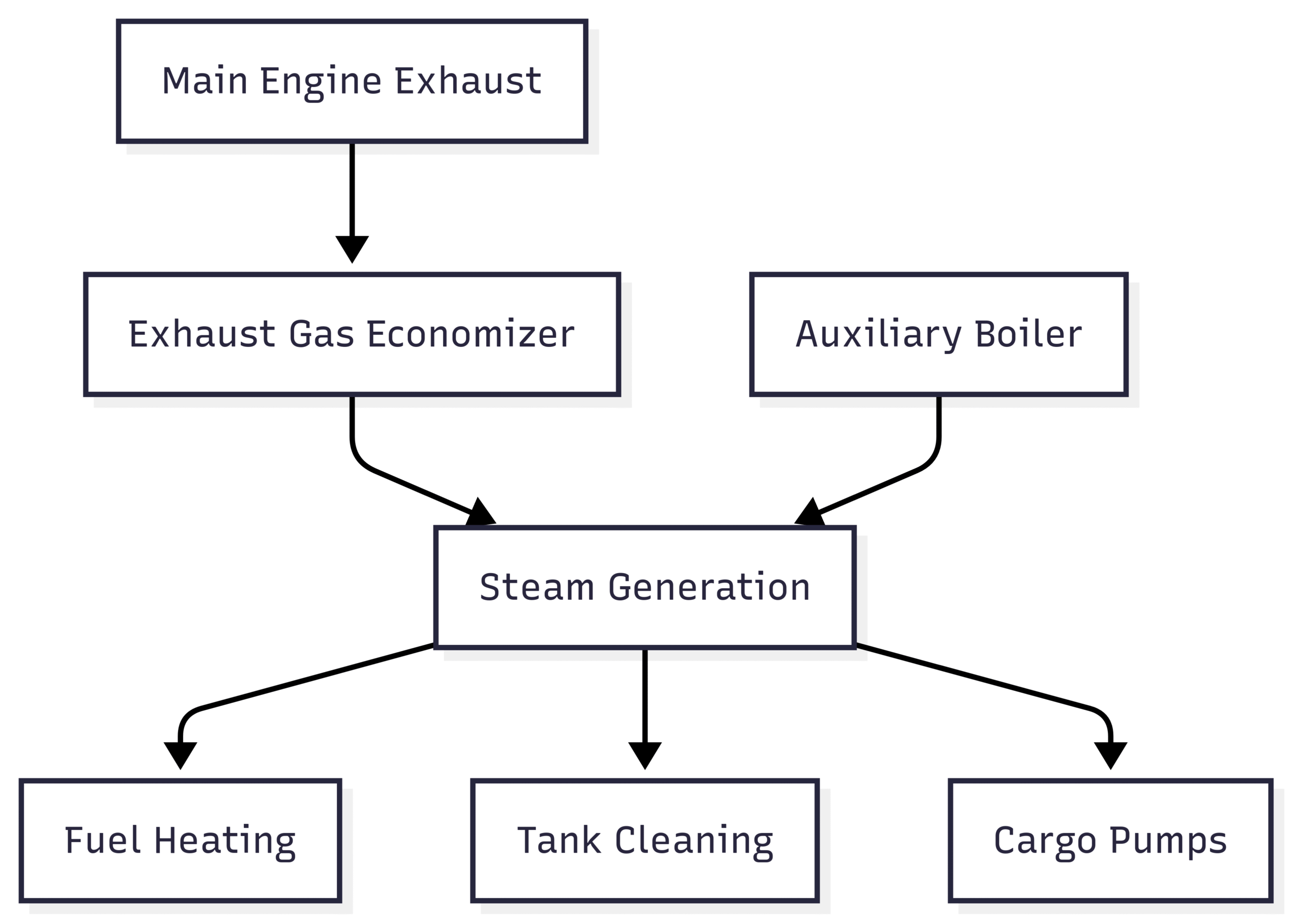
6. Sewage Treatment Plants: Environmental Compliance
Sewage treatment plants process blackwater (toilet waste) and greywater (from galleys and showers) to meet MARPOL Annex IV standards. Untreated discharge is prohibited within 12 nautical miles of land.
Technologies
- Biological Aerobic Digestion: Uses bacteria to break down waste.
- Membrane Bioreactors (MBR): Combine filtration and biological treatment.
- Disinfection: Chlorination or UV treatment ensures safe discharge.
Specifications
Parameter | Typical Value |
---|---|
Capacity | 1–50 m³/day |
Power Consumption | 2–10 kW |
Discharge Standard | <1,000 fecal coliforms/100 mL |
7. Oily Water Separators (OWS): Protecting the Oceans
Oily water separators remove oil from bilge water, ensuring discharges contain less than 15 ppm of oil, per MARPOL Annex I. They are critical for avoiding environmental fines during Port State Control (PSC) inspections.
Components
- Coalescers: Merge small oil droplets for separation.
- Emulsion Breakers: Handle oil-water mixtures.
- Oil Content Meters: Monitor discharge quality.
- Automatic Stop Valves: Halt discharge if oil content exceeds 15 ppm.
Record-Keeping
The Oil Record Book (ORB) logs all bilge water operations, subject to PSC scrutiny.
Specifications
Parameter | Typical Value |
---|---|
Throughput | 0.5–10 m³/h |
Oil Content Limit | <15 ppm |
Power Consumption | 1–5 kW |
8. Shaft Generators and Auxiliary Engines: Powering the Ship
Shaft generators produce electricity from main engine rotation, while auxiliary engines (diesel generators) provide power during port stays, maneuvering, or low-speed navigation. Power Management Systems (PMS) optimize load distribution.
Environmental Benefits
Hybrid shaft generators reduce fuel consumption and NOx emissions, aligning with IMO’s decarbonization goals.
Specifications
System | Power Output | Fuel Type |
---|---|---|
Shaft Generator | 500–5,000 kW | Main engine fuel (HFO/MGO) |
Auxiliary Engine | 200–2,000 kW | MGO, LNG |
9. Steering Gear Systems: Navigating with Precision
Steering gear controls the rudder, ensuring safe navigation during port approaches, narrow channels, and emergency maneuvers. SOLAS Chapter V mandates testing within 12 hours before departure.
Types
- Ram-Type: Hydraulic pistons move the rudder.
- Rotary Vane-Type: Compact, used on smaller vessels.
Automation
Feedback sensors integrate with Electronic Chart Display and Information Systems (ECDIS) and autopilots for real-time rudder positioning.
Specifications
Parameter | Typical Value |
---|---|
Torque | 50–500 kNm |
Rudder Angle | ±35° |
Power Source | Hydraulic (10–50 kW) |
10. Refrigeration and Air Conditioning: Comfort and Cargo Preservation
Refrigeration systems preserve food and cool cargo on reefer ships, while air conditioning maintains crew comfort in tropical climates. The IMO’s Kigali Amendment pushes for eco-friendly refrigerants like R-744.
Refrigerants
Refrigerant | Status | Global Warming Potential (GWP) |
---|---|---|
R-134a | Phasing out | 1,430 |
R-407C | Transitional | 1,774 |
R-744 (CO2) | Eco-friendly | 1 |
Specifications
System | Cooling Capacity | Power Consumption |
---|---|---|
Refrigeration | 10–500 kW | 5–200 kW |
Air Conditioning | 50–1,000 kW | 20–400 kW |
Real-World Case Study: Preventing Disaster
An offshore supply vessel faced a fuel contamination crisis mid-voyage. The purifier’s automated system detected high water content, halting fuel flow. A 3rd engineer’s manual intervention, guided by alarms, prevented engine stalling and a potential blackout. This incident underscores the value of automation and crew training in auxiliary system management.
Pricing Insights
Marine auxiliary machinery costs vary by vessel size and system complexity. Below are approximate price ranges for key systems (new installations, excluding maintenance):
System | Price Range (USD) |
---|---|
Marine Pump (Centrifugal) | $5,000–$50,000 |
Purifier | $20,000–$100,000 |
Air Compressor | $10,000–$80,000 |
Freshwater Generator (RO) | $50,000–$200,000 |
Oily Water Separator | $15,000–$70,000 |
Auxiliary Engine | $100,000–$500,000 |
Note: Prices depend on brand (e.g., Alfa Laval, Wärtsilä), capacity, and customization. Contact manufacturers for precise quotes.
Frequently Asked Questions (FAQ)
Are all auxiliary systems required on every vessel?
How often are auxiliary systems inspected?
What certifications govern auxiliary machinery operation?
Can auxiliary system failures lead to vessel detention?
Are newer ships more automated?
Conclusion: The Unsung Heroes of Maritime Success
Marine auxiliary machinery systems are the backbone of ship operations, ensuring propulsion, safety, and compliance. From pumps circulating vital fluids to purifiers safeguarding engines, these systems demand precision engineering and diligent maintenance. As ships embrace automation and greener technologies, auxiliary machinery will continue to evolve, driving the maritime industry toward a safer, more sustainable future.
For engineers and ship operators, mastering these systems is non-negotiable. Explore resources like MaritimEducation.com for training, schematics, and certification prep to elevate your expertise.
Happy Boating!
Share Top 10 Marine Auxiliary Machinery Systems Explained with your friends and leave a comment below with your thoughts.
Read Top 10 Engine Room Emergencies and How to Handle Them until we meet in the next article.