Discover the top 10 fuel system problems on modern ships, from contamination to pump failures, and learn preventive measures to ensure maritime efficiency.
Modern ships, from massive container vessels to agile recreational boats, rely on intricate fuel systems to power their engines, generators, and auxiliary systems. These systems are the lifeblood of maritime operations, ensuring propulsion and operational reliability across vast oceans. However, fuel system issues can lead to inefficiencies, costly repairs, or even catastrophic failures, jeopardangering safety and environmental compliance. With the maritime industry adapting to stricter regulations like the IMO 2020 sulfur cap, new fuels such as Very Low Sulfur Fuel Oil (VLSFO) and biofuels introduce both opportunities and challenges. According to the International Chamber of Shipping (ICS) and DNV, over 40% of shipboard machinery failures are linked to fuel system problems. This article dives into the top 10 fuel system issues on modern ships, their causes, impacts, and actionable solutions to keep vessels running smoothly.
The Importance of Fuel System Integrity
The fuel system of a modern ship is a complex network involving bunkering, storage, purification, and delivery to engines. Any disruption—be it contamination, mechanical failure, or improper handling—can cascade into reduced performance, engine shutdowns, or safety hazards. The shift to low-sulfur fuels and alternative blends, driven by MARPOL Annex VI regulations, has introduced new variables. Fuels like VLSFO and Marine Gas Oil (MGO) reduce emissions but can be less stable, leading to issues like sludge formation, microbial growth, and compatibility challenges. For recreational boaters, ethanol-blended fuels exacerbate problems due to their tendency to absorb water and degrade over time. Understanding these issues is critical for operators, engineers, and boat owners to maintain reliability and compliance.
Top 10 Fuel System Problems and Solutions
1. Fuel Contamination (Water, Sludge, Particulates)
Fuel contamination is the most common issue affecting marine engines, and it poses serious operational and maintenance risks. Contamination can originate from several sources:
Water Contamination
Water is the most frequent contaminant and can enter fuel systems through:
- Condensation in partially filled tanks (due to temperature changes)
- Leaky fuel caps or vents
- Contaminated bunkering (fuel supply) operations
Once water is in the system, it can lead to phase separation, especially in ethanol-blended fuels (common in small boats). Ethanol attracts water and can separate from fuel, settling at the bottom of the tank where the fuel pickup is—leading to:
- Poor engine performance
- Potential damage
Sludge, Sediment, and Rust
These contaminants come from:
- Degraded fuel sitting too long in tanks (common in infrequently used vessels)
- Older tanks with corrosion and scale
- Low-quality fuel without proper pre-treatment
When these contaminants accumulate, they clog fuel filters and injectors, starving the engine of fuel and possibly leading to failure.
Impact of Fuel Contamination
Problem | Consequence |
---|---|
Poor combustion | Misfires, rough idling, reduced fuel efficiency |
Corrosion | Damage to injectors, pumps, and metal fuel system parts |
Clogged filters/injectors | Fuel starvation, sudden engine shutdown |
Increased maintenance costs | Frequent filter replacements, fuel system repairs |
Real-World Example
In 2018, over 100 ships faced severe fuel system failures after bunkering contaminated VLSFO (Very Low Sulfur Fuel Oil) in Houston and Singapore. The contaminated fuel caused widespread filter clogging and engine problems, underlining the importance of fuel quality testing.
Solutions & Best Practices
Method | Description |
---|---|
Regular Tank Maintenance | Drain water from settling tanks or separators regularly. Clean sludge buildup. |
Fuel Sampling & Testing | Use lab analysis (e.g., ASTM D4740) to check for compatibility and stability. |
Purification Systems | Install centrifugal separators or fine micron filters to clean fuel. |
Additives (for boats) | Use products like Quicksilver Quickare to combat water, corrosion, and oxidation. |
Table: Common Contaminants & Their Effects
Contaminant | Source | Effect | Mitigation |
---|---|---|---|
Water | Condensation, leaks | Corrosion, misfires, phase separation | Fuel-water separators, ethanol-safe additives |
Sludge | Degraded fuel | Clogged filters, injector fouling | Tank cleaning, fuel stabilizers |
Particles | Rust, debris from tanks | Wear on injectors and pumps | Fine inline filters, regular inspections |
2. Fuel Incompatibility (VLSFO Blending Issues)
With the IMO 2020 regulation limiting sulfur content in marine fuel to 0.5%, many suppliers began offering Very Low Sulfur Fuel Oil (VLSFO). However, VLSFO is not a single standard fuel—it is often blended from various refinery streams, such as:
- Light cycle oils
- Residual fuels
- Aromatic-rich stocks
These components differ significantly in chemical makeup, which creates a risk: when mixed with another batch of VLSFO, the fuels may become incompatible.
What Happens?
- Incompatible blends cause asphaltenes (heavy organic molecules) to precipitate out of the fuel.
- These asphaltenes form sludge-like deposits, especially in filters, fuel lines, and injectors.
- This sludge does not burn and can severely disrupt fuel flow.
Impact of VLSFO Incompatibility
Issue | Effect |
---|---|
Asphaltene precipitation | Clogs fuel filters, injectors, and separators |
Overloaded fuel pumps | Pumps work harder due to restricted flow, increasing wear and risk |
Engine derating | Reduced engine power output due to restricted combustion |
Maintenance increase | More frequent filter changes and injector cleaning |
Possible engine failure | In severe cases, engines may shut down due to fuel starvation |
Real-World Risk
This issue is especially critical for ships with tight turnaround schedules. If incompatible fuel is bunkered without testing, clogging can occur within hours, leading to delays, emergency repairs, or even loss of propulsion—posing a safety risk at sea.
Solutions & Best Practices
Solution | Description |
---|---|
Pre-Bunkering Testing | Perform compatibility tests before mixing fuels. Spot tests like the ASTM D4740 “spot test” can detect asphaltene instability. |
Segregated Storage | Store each VLSFO batch in separate tanks until compatibility is confirmed. Never mix unknown blends. |
Monitoring | Regularly monitor fuel filter pressure differentials. A rising pressure drop often signals filter clogging due to sludge. |
Use Purifiers Properly | Set purifiers for optimal temperature and flow to remove sludge efficiently. |
Fuel incompatibility isn’t just a theoretical risk—it’s a daily operational hazard for vessels using VLSFO. As the marine fuel landscape evolves, compatibility testing, fuel segregation, and proactive monitoring are key to avoiding catastrophic failures and keeping engines running smoothly.
Chart: Fuel Incompatibility Workflow
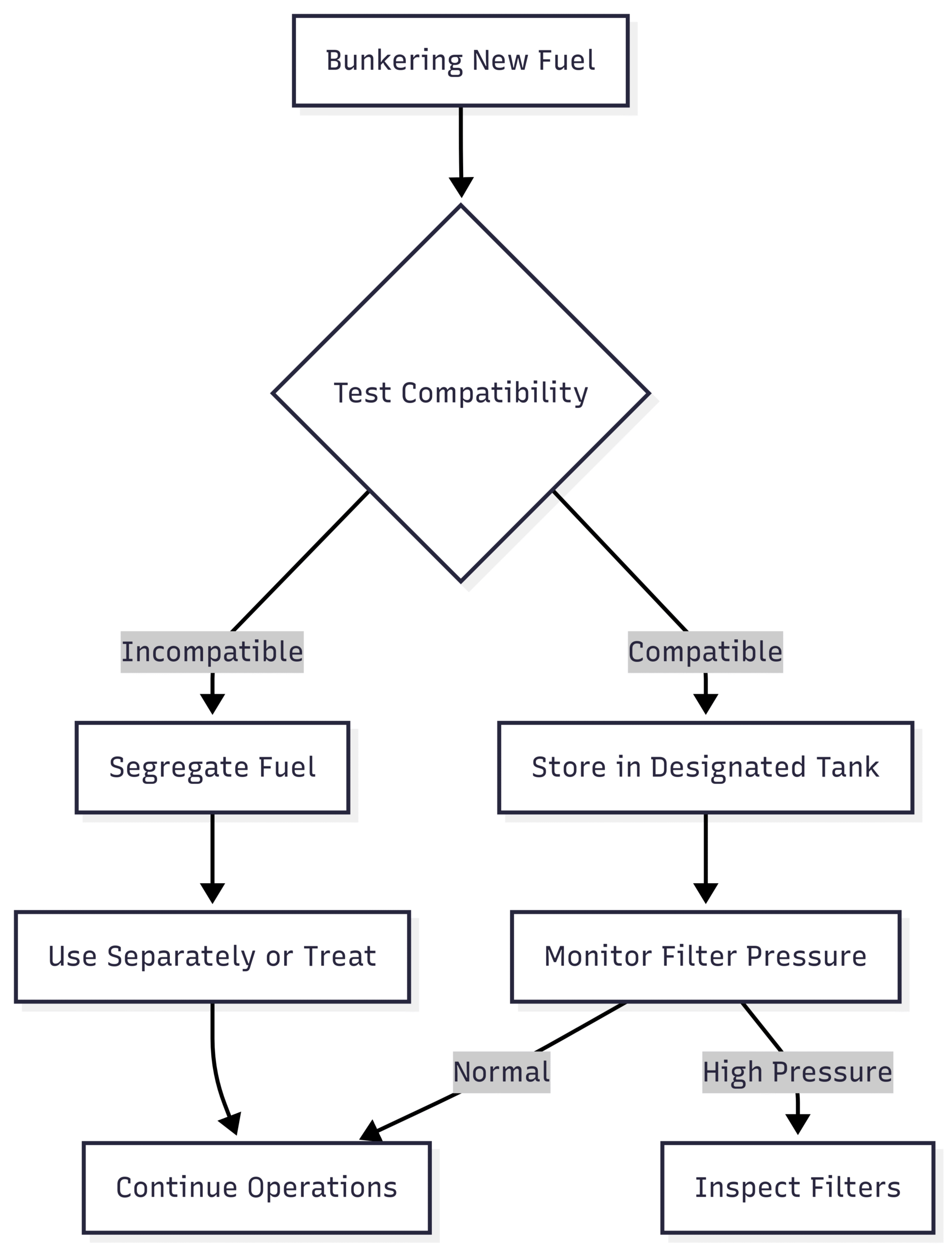
3. Poor Fuel Viscosity Control
Modern fuel injection systems—especially in marine diesel engines—depend on precise fuel viscosity to operate efficiently. Viscosity is a measure of a fluid’s resistance to flow, and for fuel, it’s crucial to keep it within an optimal range (typically 10–15 centistokes or cSt) at the injection temperature (often around 130–150°C for HFO).
When viscosity is too high:
- The fuel is too thick.
- It doesn’t atomize properly—that is, it doesn’t break into fine droplets when injected into the combustion chamber.
- This leads to incomplete combustion, carbon buildup, and smoky exhaust.
When viscosity is too low:
- The fuel is too thin.
- It can fail to lubricate fuel pumps properly, causing premature wear and damage to injectors and pumps.
So, poor viscosity control affects both combustion efficiency and mechanical reliability.
Causes of Viscosity Problems
- Malfunctioning Viscosity Regulators
These are automatic systems designed to adjust the fuel’s temperature to reach the correct viscosity. If the sensor or controller malfunctions, the system won’t adjust properly. - Inaccurate Steam Heater Controls
Viscosity is temperature-dependent: higher temperatures lower the fuel’s viscosity. If the fuel heating system is faulty, it may overheat or underheat the fuel, resulting in viscosity that’s outside the acceptable range. - Abrupt Fuel Changeovers (e.g., from HFO to MGO)
Switching between different fuel types—especially heavy fuel oil (HFO) and marine gas oil (MGO)—without gradual temperature and viscosity adjustment can lead to a sudden drop or spike in viscosity. MGO, for instance, has naturally lower viscosity and needs less heating.
Impact of Poor Viscosity Control
- Poor Atomization
Leads to larger fuel droplets, causing incomplete combustion, reduced power, and increased emissions (e.g., soot, smoke, unburned hydrocarbons). - Pump and Injector Damage
Thin fuel (low viscosity) doesn’t lubricate well. This can cause increased friction, overheating, and wear of moving parts in the fuel injection system. - Reduced Engine Efficiency and Reliability
Engine output can become unstable, and long-term engine health is compromised.
Solutions
- Install Automatic Viscosity Control Units
These systems continuously measure the viscosity of the fuel and adjust its temperature using a steam or electric heater to maintain it in the optimal range. Modern ships are usually equipped with these. - Monitor Fuel Temperature During Startup and Load Changes
Manual oversight is still crucial, especially during variable load conditions. Ensure that fuel temperature changes gradually to avoid thermal shock and viscosity swings. - Calibrate Heaters Regularly
Regularly check and calibrate your steam heaters and thermostatic valves to make sure they respond accurately and quickly to maintain desired viscosity levels.
Summary
Aspect | Details |
---|---|
Ideal Viscosity Range | 10–15 cSt at injection point |
Main Risk if Too High | Poor atomization → inefficient combustion |
Main Risk if Too Low | Insufficient lubrication → pump/injector wear |
Primary Causes | Faulty regulators, heaters, or rapid fuel switch |
Key Fixes | Auto viscosity controllers, heater calibration, careful monitoring |
4. Fuel Pump Wear or Seizure
High-pressure fuel pumps are essential for delivering consistent fuel to marine engines, especially in modern high-efficiency systems. However, they are precision components that are highly sensitive to:
- Abrasive contaminants (e.g., rust, dust, debris)
- Poor lubrication from fuel with inadequate viscosity or additives
- Neglected maintenance, especially overdue overhauls
Even minor contamination or wear can lead to catastrophic pump failure, affecting engine reliability and safety.
Impact of Fuel Pump Wear
Issue | Effect |
---|---|
Loss of fuel pressure | Engine stalls, reduced power, or failure to start |
Impaired injection timing | Incomplete combustion, increased emissions, and misfires |
Seizure of internal parts | Total pump failure requiring expensive repairs or replacements |
Increased maintenance costs | Due to emergency repairs or system-wide fuel contamination risks |
Solutions & Preventative Measures
Solution | Description |
---|---|
Inline Duplex Filters | Install fine-particle fuel filters (e.g., 10–30 microns) to trap abrasives before fuel reaches the pump. |
Monitor Pump Pressure Logs | Regular pressure readings help detect pump degradation early (i.e., gradual pressure drop). |
Follow OEM Maintenance | Stick to manufacturer-recommended overhaul intervals and lubrication checks. |
Use Quality Fuel | Ensure fuel has proper lubricity, especially for ULSD (Ultra Low Sulfur Diesel), which may need additives. |
Table: Fuel Pump Failure – Causes & Fixes
Cause | Symptom | Fix |
---|---|---|
Abrasive particles | Plunger scoring, wear | Install inline duplex/fine filters |
Poor lubrication | Pump seizure, heat rise | Use compatible, lubricated fuels |
Overdue maintenance | Internal leaks, pressure drop | Perform regular pump overhauls |
Marine fuel pumps operate under high stress and tight tolerances. Even microscopic contaminants or lubrication failures can lead to serious engine issues. A proactive maintenance approach—including proper filtration, monitoring, and adherence to service intervals—ensures longer pump life and avoids costly downtime.
5. Microbial Growth (“Diesel Bug”)
Microbial contamination—commonly referred to as the “diesel bug”—is caused by the growth of bacteria, fungi, and yeast in marine fuel tanks. These microbes thrive at the fuel-water interface, especially in:
- Partially filled tanks (where condensation forms)
- Biofuels or blends (which have higher water affinity)
- Warm, humid storage conditions
They feed on hydrocarbons and reproduce rapidly, especially when water is present.
Impact of Microbial Growth
Issue | Effect |
---|---|
Acidic byproducts | Corrode steel tanks and fuel system components |
Biomass accumulation | Forms sludge that blocks filters and lines |
Fuel degradation | Lowers combustion quality and can lead to engine misfires |
Equipment damage | Long-term exposure can damage injectors and pumps |
Real-World Notes
This problem is especially severe during long voyages or seasonal layups where fuel remains static. Biofuels, though eco-friendly, are more prone to microbial contamination due to higher oxygen and water absorption.
Solutions & Best Practices
Solution | Description |
---|---|
Use Biocides | Add fuel biocides during long storage periods or voyages to kill microbes |
Tank Cleaning | Periodically clean tanks to remove microbial sludge from tank bottoms |
Keep Tanks Full | Minimize condensation by keeping fuel tanks as full as possible |
Monitor Water Levels | Use water detection paste or separators to identify water early |
Fuel Polishing Systems | Circulate and filter fuel periodically to remove microbes and debris |
Environmental Note
While biofuels reduce emissions and support sustainability goals, they are biodegradable—making them more susceptible to microbial growth. This increases the need for vigilant fuel management, especially in warmer climates or long-term storage.
Table: Diesel Bug Summary
Cause | Symptom | Fix |
---|---|---|
Water presence | Microbial growth | Keep tanks full, remove water |
Warm fuel + biofuel | Sludge at fuel-water line | Use biocides, clean tanks |
Poor storage hygiene | Filter clogs, bad smell | Fuel polishing, regular inspections |
Microbial contamination may be invisible at first, but its effects can be devastating if left unchecked. Preventative fuel hygiene, especially with biofuel use, is essential for marine reliability. Regular treatment, tank maintenance, and early detection can save both money and engine health.
6. Fuel Leakage in High-Pressure Lines
Problem: Leaks in high-pressure fuel lines or pump flanges pose fire hazards and cause engine shutdowns.
Impact:
- Fuel loss
- Safety risks (fires)
- Emergency stops triggered by mist detectors
Solutions:
- Install insulation shields per SOLAS Regulation II-2/4.2.2.5.
- Regularly inspect fuel lines for wear or loose fittings.
- Monitor fuel pressure for sudden drops.
7. Improper Fuel Changeover (HFO to MGO)
Problem: Switching fuels (e.g., from HFO to MGO in Emission Control Areas) without gradual blending can cause thermal shock or viscosity mismatches.
Impact:
- Injector damage
- Airlocks or filter blockages
- Engine instability
Solutions:
- Use gradual blending during changeovers.
- Allow sufficient heating/cooling time.
- Monitor differential pressures during switching.
8. Clogged Fuel Filters and Strainers
Problem: Clogged filters are often the first sign of contamination or fuel instability, leading to increased pressure drops and engine shutdowns.
Impact:
- Reduced fuel flow
- Frequent maintenance
- Unexpected engine failures
Solutions:
- Use duplex filters for seamless changeovers.
- Conduct weekly filter inspections.
- Track pressure differential trends.
9. Air in Fuel Lines
Problem: Air bubbles disrupt fuel pressure and combustion, often caused by suction leaks, incomplete priming, or faulty seals.
Impact:
- Engine misfiring
- Irregular RPM
- Starting difficulties
Solutions:
- Bleed fuel lines before startup, especially after maintenance.
- Inspect O-rings and flanges for wear.
- Use the Racor bowl as a sight glass to detect bubbles.
Case Study: A container ship in the Mediterranean faced engine stoppage due to air pockets from poor priming during a VLSFO changeover, narrowly avoiding grounding through quick engineer intervention.
10. Incorrect Purifier Operation
Problem: Centrifugal purifiers, critical for removing water and sludge, can fail due to incorrect settings or maintenance.
Impact:
- Poor fuel separation
- Sludge buildup in engines
- Reduced fuel quality
Solutions:
- Train engineers on purifier optimization per OEM guidelines.
- Use correct gravity disc sizing.
- Schedule regular purifier disassembly and cleaning.
Chart: Purifier Operation Workflow
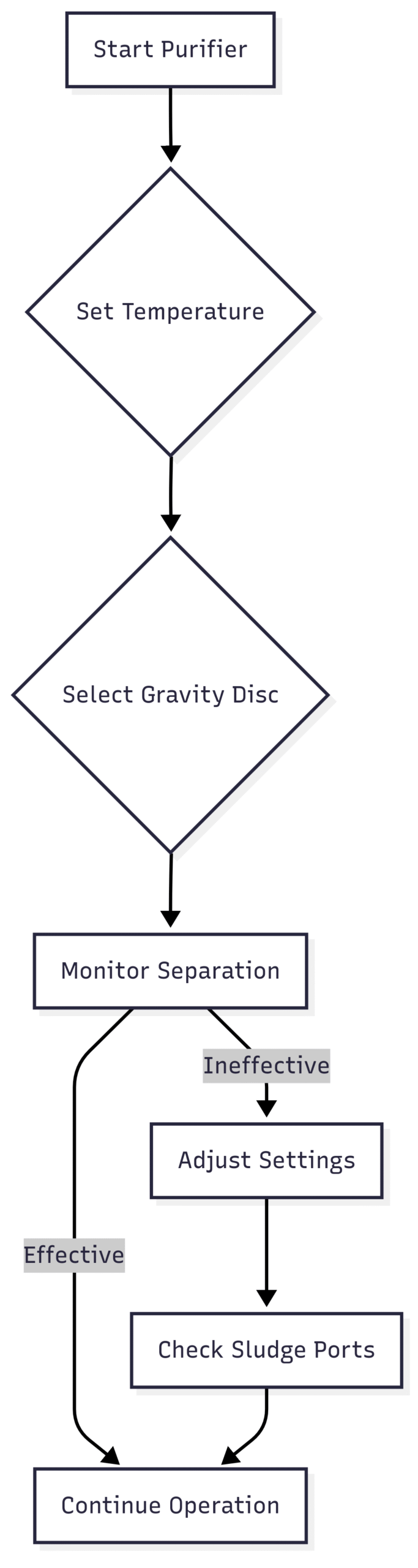
Preventive Maintenance Strategies
Preventing fuel system problems requires a proactive approach. Key strategies include:
- Regular Inspections: Check filters, pumps, and lines weekly for wear, leaks, or blockages.
- Fuel Quality Control: Source fuel from reputable suppliers and test before bunkering.
- Additives: Use stabilizers (e.g., Quicksilver Quickstor) for long-term storage and treatments (e.g., Quickare) for regular use.
- Training: Ensure engineers are trained per STCW A-III/1 standards for purifier and fuel system management.
- Monitoring Systems: Install fuel flow meters to track consumption and detect leaks, aiding IMO DCS and SEEMP compliance.
Table: Recommended Fuel Additives
Product | Use Case | Benefits |
---|---|---|
Quicksilver Quickare | Every fill-up | Controls corrosion, cleans deposits |
Quicksilver Quickleen | Periodic cleaning | Removes carbon deposits, extends spark plug life |
Quicksilver Quickstor | Storage | Prevents fuel oxidation, stabilizes for up to a year |
Real-World Lessons from Fuel System Failures
A recreational boater’s two-month struggle with a Westerbeke engine illustrates the complexity of diagnosing fuel issues. The engine exhibited RPM drops and stalling, initially attributed to fuel starvation. After replacing filters, cleaning tanks, and checking for water, the issue persisted. Eventually, a tiny crack in a fuel hose near the pump was identified, allowing air to enter the system. This case underscores the importance of:
- Patience in Troubleshooting: Air leaks can be subtle and require meticulous inspection.
- Teamwork: Involving crew with keen observation skills can uncover hidden issues.
- Comprehensive Checks: Even “insignificant” imperfections, like a loose Racor port plug or a hairline hose crack, can cause major problems.
FAQs
What is the most common fuel-related problem on ships?
Can fuel problems be completely avoided?
How do you test for fuel compatibility?
What role does a fuel flow meter play?
Are biofuels safer than traditional fuels?
Conclusion
Fuel system problems on modern ships, from contamination to mechanical failures, pose significant challenges to operational reliability and safety. As marine fuels evolve to meet environmental regulations, operators must adapt to new complexities like VLSFO instability and biofuel vulnerabilities. By prioritizing regular maintenance, using high-quality fuels and additives, and training crews effectively, ship operators and recreational boaters can mitigate risks and ensure smooth operations. A well-maintained fuel system not only enhances performance but also supports compliance with global standards, safeguarding both the vessel and the environment.
Happy Boating!
Share Top 10 Fuel System Problems on Modern Ships with your friends and leave a comment below with your thoughts.
Read The top five trends in marine propulsion until we meet in the next article.