Learn how to manage the top 10 engine room emergencies on ships, from fires to blackouts, with expert strategies and safety tips.
The engine room is the heart of any vessel, powering its journey across vast oceans. But this critical space, packed with high-pressure systems, flammable fuels, and complex machinery, is also a hotspot for emergencies. From raging fires to sudden blackouts, engine room crises demand swift, decisive action to protect the crew, the ship, and the environment. According to the International Maritime Organization (IMO), engine room fires account for over 60% of shipboard fires, often resulting in millions of dollars in damages and, tragically, loss of life. This comprehensive guide explores the top 10 engine room emergencies, offering practical strategies, regulatory insights, and real-world lessons to ensure maritime safety.
Why Engine Room Emergency Preparedness Matters
The engine room operates under extreme conditions: temperatures soar above 200°C, fuel systems handle pressures exceeding 20 bar, and rotating machinery runs non-stop. These factors create a volatile environment where a single spark or leak can escalate into a catastrophe. The International Union of Marine Insurance (IUMI) reports that human error, poor maintenance, and delayed detection are leading causes of engine room incidents—most of which are preventable with proper training and preparedness.
The stakes are high. A mishandled emergency can lead to vessel detentions, environmental disasters, or worse. The 2020 Maersk Honam fire, which claimed five lives and destroyed cargo worth millions, began in the engine room due to a fuel leak igniting on a hot surface. Such incidents underscore the need for robust safety protocols aligned with the IMO’s Standards of Training, Certification, and Watchkeeping (STCW) Code and the International Convention for the Safety of Life at Sea (SOLAS).
This guide equips marine engineers, crew members, and ship operators with actionable strategies to recognize, respond to, and recover from engine room emergencies. By combining regulatory requirements, real-world examples, and practical tips, it aims to foster a culture of safety and readiness.
Understanding the Engine Room Risk Environment
Engine rooms are confined spaces filled with hazards:
- Flammable Materials: Fuel oils, lubricants, and hydraulic fluids are omnipresent.
- Ignition Sources: Hot surfaces, electrical faults, and sparks from machinery.
- Confined Spaces: Limited escape routes increase risks during emergencies.
- High-Pressure Systems: Fuel and steam lines pose explosion risks if compromised.
Modern vessels rely on automation for monitoring, but human vigilance remains critical. STCW Section A-III/1 mandates that engine room personnel undergo rigorous training in emergency response, while SOLAS Chapter II-2 requires fire prevention and control systems to be maintained and tested regularly. Regular drills, clear communication, and proper Personal Protective Equipment (PPE) are non-negotiable for safe operations.
Top 10 Engine Room Emergencies and Response Strategies
Below are the ten most common engine room emergencies, their causes, and step-by-step response protocols, enriched with regulatory references and real-world insights.
1. Engine Room Fire
Causes: Fuel leaks onto hot surfaces (SOLAS Reg. II-2/4.2.2.5), electrical short circuits, or crankcase explosions.
Risks: Rapid spread due to abundant fuel and oxygen, potential for crew fatalities, and extensive damage.
Response Strategy:
- Sound the general alarm and notify the bridge and chief engineer.
- Stop ventilation systems and close dampers to starve the fire of oxygen.
- Isolate fuel supply lines to prevent further combustion.
- Use portable extinguishers (CO₂ or foam) for small fires.
- Deploy fixed CO₂ or water mist systems for larger fires, ensuring crew evacuation first.
- Initiate boundary cooling to protect adjacent compartments.
- Muster crew and prepare for possible evacuation.
Real-World Example: The 2020 Maersk Honam fire in the Indian Ocean began with a fuel leak igniting in the engine room. Delayed detection led to an uncontrollable blaze, highlighting the need for early alarm systems and trained response teams.
Preventive Tip: Regular maintenance of fuel lines and electrical systems, coupled with fire detection sensors, can reduce risks. SOLAS mandates flame detectors and smoke alarms in engine rooms.
2. Main Engine Failure or Shutdown
Causes: Lubrication failure, scavenge fires, over-speed, or control system malfunctions.
Risks: Loss of propulsion in busy shipping lanes, potential collisions, or grounding.
Response Strategy:
- Shift propulsion control to manual mode.
- Isolate the issue (e.g., check crankcase pressure or oil levels).
- Notify the bridge immediately for course or speed adjustments.
- Switch to standby generators to maintain auxiliary power.
- Engage standby propulsion systems, if available.
- Conduct temporary repairs only if safe, following lockout-tagout procedures.
Regulatory Reference: IMO Model Course 7.02 requires engineers to practice emergency propulsion drills.
Real-World Example: In 2021, a Panamax bulk carrier in the Singapore Straits avoided a blackout when a third engineer manually started a standby fuel pump within 60 seconds of a main engine shutdown. Routine drills were credited for the swift response.
3. Engine Room Flooding
Causes: Sea water ingress via leaking sea chests, hull breaches, or burst pipes.
Risks: Engine damage, electrical short circuits, and vessel instability.
Response Strategy:
- Activate bilge pumps and sound bilge alarms.
- Close sea suction valves to stop ingress.
- Deploy portable submersible pumps for rapid water removal.
- Monitor vessel stability and report to the bridge.
- Switch to emergency power if water threatens electrical systems.
- Apply temporary patches or clamps to breached areas.
Preventive Tip: Regular ultrasonic testing of pipes and hull integrity can detect weak points. Brightly painted bilges make leaks easier to spot.
Regulatory Note: SOLAS Chapter II-1 requires watertight compartments and bilge systems to be inspected regularly.
4. Boiler Furnace Explosion
Causes: Accumulated unburned fuel, faulty purging, or ignition failure.
Risks: Severe structural damage and crew injuries due to high-pressure blasts.
Response Strategy:
- Shut down the burner immediately.
- Sound the alarm and secure the boiler area.
- Ventilate the furnace to clear residual fuel vapors.
- Isolate fuel lines and use emergency shutdown buttons.
- Inspect relief valves and explosion doors post-incident.
Regulatory Note: SOLAS Chapter II-2 mandates pressure relief valves and explosion doors on boilers.
Preventive Tip: Strict adherence to purging protocols before ignition can prevent fuel buildup.
5. Crankcase Explosion
Causes: Oil mist ignition from overheated bearings or piston components.
Warning Signs: High crankcase temperatures, audible knocking, oil mist detector alarms.
Response Strategy:
- Shut down the engine immediately.
- Wait at least 30 minutes before opening crankcase doors to prevent oxygen fueling a fire.
- Engage CO₂ if fire is detected.
- Analyze oil mist detector logs to identify trends.
- Conduct bearing inspections post-incident.
Regulatory Requirement: SOLAS II-1 mandates oil mist detectors and relief valves on engines above 2,250 kW.
Preventive Tip: Regular lubrication analysis and temperature monitoring can detect issues early.
6. Blackout (Total Power Failure)
Causes: Generator failure, fuel supply interruption, short circuits, or breaker trips.
Risks: Loss of critical systems (steering, navigation, fire pumps), increasing collision risks.
Response Strategy:
- Start the emergency generator (SOLAS requires activation within 45 seconds).
- Shift to manual power distribution.
- Restore critical systems: steering gear, ECDIS, fire pumps.
- Identify and isolate the fault before restoring full power.
- Log the incident and review generator maintenance schedules.
Training Note: STCW requires blackout recovery drills, especially on Unmanned Machinery Space (UMS) vessels.
Preventive Tip: Test emergency generators weekly and ensure fuel lines are free of blockages.
7. Steering Gear Failure
Causes: Hydraulic leaks, electrical faults, or mechanical jams.
Risks: Loss of vessel control, particularly in confined waters.
Response Strategy:
- Activate the manual hydraulic pump.
- Switch to emergency steering gear.
- Communicate heading changes to the bridge via sound-powered phone.
- Inspect rudder angle feedback and linkages.
- Repair primary systems only when safe.
Regulatory Requirement: SOLAS Chapter V/26 mandates emergency steering gear activation within 45 seconds.
Preventive Tip: Regular hydraulic fluid checks and linkage inspections can prevent failures.
8. Fuel Oil Leak
Causes: High-pressure fuel line ruptures, loose flanges, or worn gaskets.
Risks: Fire hazard, environmental pollution, and crew exposure to toxic fumes.
Response Strategy:
- Shut off the fuel pump or isolate the leaking section.
- Use oil-absorbent pads and drip trays to contain the spill.
- Eliminate ignition sources (e.g., stop hot work).
- Ventilate the area and clean up the spill.
- Log and report the incident per MARPOL Annex I.
Real-World Example: A fuel leak on the MSC Flaminia in 2012 ignited, causing a fire that killed crew members and destroyed cargo. Routine pipe inspections could have prevented the tragedy.
Preventive Tip: Conduct pressure and tightness tests on fuel lines regularly, especially when switching to ultra-low-sulfur fuels, which are more leak-prone.
9. High Jacket Water or Lube Oil Temperature
Causes: Cooling water failure, low oil levels, fouled heat exchangers, or pump malfunctions.
Risks: Engine overheating, reduced efficiency, or component damage.
Response Strategy:
- Reduce engine load to lower temperatures.
- Check pump operation and valve alignments.
- Inspect and clean heat exchangers.
- Top up coolant or oil levels if needed.
- Monitor trends to identify recurring issues.
Monitoring Note: STCW watchkeeping routines require temperature checks every 30 minutes at sea.
Preventive Tip: Schedule heat exchanger cleanings and maintain spare coolant onboard.
10. Burst Pipe or Valve Failure
Causes: Overpressure, metal fatigue, or improper maintenance.
Risks: Flooding, fuel leaks, or steam burns.
Response Strategy:
- Shut the relevant isolation valve immediately.
- Apply pipe clamps or patches for temporary repairs.
- Notify the bridge and chief engineer.
- Initiate a bypass if feasible.
- Wear PPE to protect against burns or slips.
Preventive Tip: Lag steam and fuel pipes to prevent overheating, and inspect insulation regularly.
Real-World Lesson: The Value of Vigilance
A personal account from a Nordhavn 40 trawler owner illustrates the importance of proactive safety measures. During a routine cruise from San Diego to Dana Point, the owner noticed a cloud of exhaust in the engine room through a small window in the door—a feature initially deemed unnecessary but added at the insistence of a sales representative. The exhaust stemmed from a blown gasket in the dry stack exhaust system. By opening windows and doors to ventilate the area, the owner safely continued the journey without incident. The window allowed early detection, preventing a potential fire had the door been opened blindly, introducing oxygen to a smoldering hazard. This story underscores the value of simple safety features and regular checks.
Building a Safety Management System (SMS) for the Engine Room
A robust SMS is the backbone of engine room safety, providing clear protocols to mitigate risks. Key components include:
- PPE Requirements: Anti-slip shoes, helmets, gloves, eyewear, and coveralls.
- Emergency Procedures: Defined roles for each crew member during crises.
- Equipment Capacities: Safe working loads for lifts and circuit limits to prevent overloads.
- Incident Documentation: Protocols for logging accidents and near misses.
- Communication Channels: Clear workflows between engine room, bridge, and shore personnel.
- Environmental Compliance: Adherence to MARPOL and flag state regulations for waste disposal.
Waste Management Protocols
Improper disposal of oily rags, bilge water, or sludge can ignite fires or violate environmental laws. Best practices include:
- Oily Rags: Store in designated fire-resistant containers and incinerate or dispose of at port.
- Bilge Water: Use an oily water separator (OWS) to filter greywater, storing sludge in dedicated tanks.
- Solid Waste: Retain in stainless steel tanks until land disposal is available.
Fire Prevention Measures
- Conduct pressure and tightness tests on fuel pipes.
- Lag steam and fuel pipes to prevent overheating.
- Install drip trays under potential leak points.
- Maintain emergency water nozzles for fire suppression.
Chart: Engine Room Emergency Response Workflow
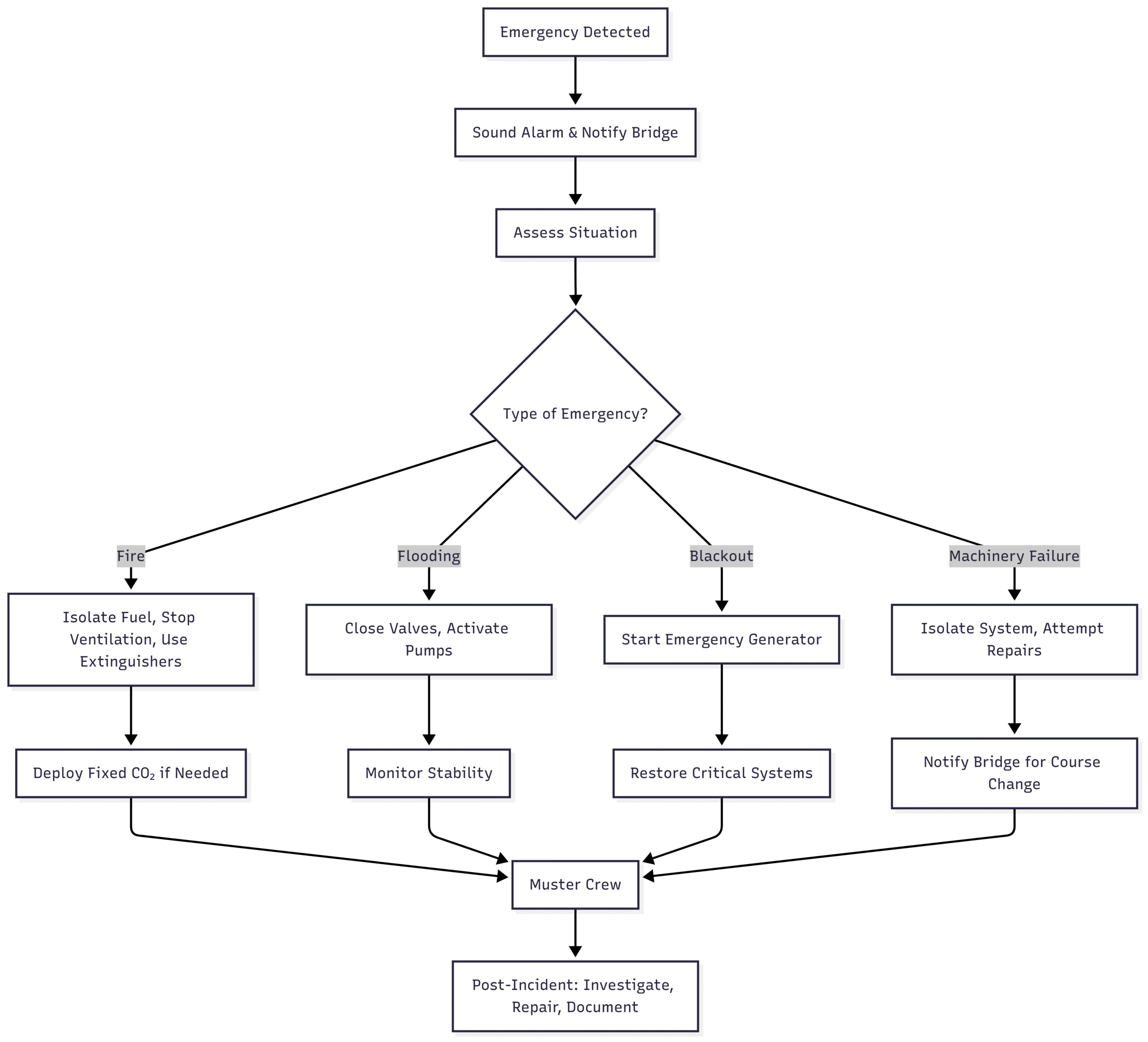
Training and Drills: The Key to Readiness
STCW courses, such as Basic Safety Training (VI/1), Advanced Firefighting (VI/3), and Engine Resource Management (ERM), equip crews with essential skills. SOLAS and the International Safety Management (ISM) Code mandate monthly fire and blackout drills to ensure familiarity with procedures. Regular simulations improve response times and build confidence under pressure.
Table: Recommended Training for Engine Room Personnel
Training Course | STCW Reference | Focus Area | Frequency |
---|---|---|---|
Basic Safety Training | VI/1 | Firefighting, survival techniques | Every 5 years |
Advanced Firefighting | VI/3 | Fire control, BA team coordination | Every 5 years |
Engine Resource Management | A-III/1 | Teamwork, emergency decision-making | Initial |
Blackout Recovery Drills | ISM Code | Power restoration, critical systems | Monthly |
Frequently Asked Questions (FAQ)
What is the most dangerous engine room emergency?
Fires and crankcase explosions pose the greatest risks due to their rapid escalation and confined escape routes.
How often should emergency drills be conducted?
SOLAS and ISM Code require monthly fire and blackout drills with full crew participation.
Are engine room emergencies logged?
Yes, all incidents, including near misses, must be recorded in the engine room logbook and reported to the company’s SMS.
Can automation prevent all emergencies?
No, automation aids early detection, but trained human response is critical for effective crisis management.
What PPE is required in the engine room?
Anti-slip shoes, helmets, gloves, protective eyewear, and coveralls are mandatory.
Conclusion: Preparedness Saves Lives
Engine room emergencies are a reality of maritime operations, striking without warning and testing the mettle of every crew member. Whether it’s a fuel leak sparking a fire or a blackout threatening navigation, the difference between recovery and disaster lies in preparation. By mastering response strategies, adhering to SOLAS and STCW standards, and fostering a culture of safety through training and drills, crews can navigate even the most dire situations.
The U.S. Coast Guard’s call to “Boat Responsibly” extends to engine room operations. Equip your team with the knowledge and tools to combat hazards, from oily rags to burst pipes. Visit resources like MaritimEducation.com or MITAGS for checklists, training programs, and simulation-based learning to strengthen your readiness. In the engine room, professionalism means expecting the unexpected—and being ready to bring your ship and crew safely home.
Happy Boating!
Share Top 10 Engine Room Emergencies and How to Handle Them with your friends and leave a comment below with your thoughts.
Read Top 10 Fuel System Problems on Modern Ships until we meet in the next article.