Safe Working Practices in the Engine Room
Learn safe working practices in the engine room to ensure vessel safety, efficiency, and compliance with maritime regulations.
The engine room is the heart of any vessel, powering its propulsion, electrical systems, and auxiliary machinery. Ensuring safe working practices in this high-stakes environment is critical for the safety of the crew, the efficiency of operations, and compliance with international maritime regulations. A well-managed engine room minimizes risks, prevents accidents, and optimizes vessel performance. This comprehensive guide explores the key aspects of safe engine room operations, offering actionable insights, best practices, and strategies to create a robust safety management system (SMS).
Why Engine Room Safety Matters
The engine room is a complex and hazardous environment. It houses powerful machinery, high-pressure systems, flammable materials, and intricate electrical setups. A single oversight can lead to catastrophic consequences, such as fires, equipment failures, or crew injuries. According to the International Maritime Organization (IMO), engine room incidents account for a significant portion of maritime accidents, with fuel leaks and electrical failures being leading causes. Implementing safe working practices mitigates these risks, ensuring smooth operations and crew safety.
A robust SMS is the cornerstone of engine room safety. It provides a structured framework for managing risks, maintaining equipment, and ensuring compliance with regulations like the IMO’s International Safety Management (ISM) Code and MARPOL Annex VI. By prioritizing safety, ship operators can reduce downtime, avoid costly repairs, and protect the environment from hazardous spills.
Key Components of Engine Room Safety
Safe engine room operations rely on several interrelated components, including teamwork, communication, situational awareness, and adherence to well-defined procedures. Below, we explore these components in detail.
1. Engine Room Resource Management (ERM)
ERM is a holistic approach to managing human, technical, and operational resources in the engine room. It emphasizes leadership, communication, situational awareness, workload management, and decision-making.
- Leadership: The Chief Engineer sets the tone for safe operations, issuing standing orders and overseeing compliance. Effective leadership fosters accountability and ensures that safety protocols are followed.
- Communication: Clear, concise communication is vital in the engine room, where misunderstandings can lead to errors. Crew members must use standardized protocols, such as closed-loop communication, to confirm instructions and report issues.
- Situational Awareness: Maintaining awareness of the engine room’s operational environment enables the crew to anticipate and address potential problems. This includes monitoring machinery, environmental conditions, and crew activities.
- Workload Management: Distributing tasks evenly prevents fatigue and ensures that no crew member is overwhelmed. Proper workload management enhances focus and reduces the likelihood of errors.
- Decision-Making: Structured problem-solving and critical thinking are essential, particularly during emergencies. Crew members should follow established protocols and consult with senior officers when needed.
2. Teamwork and Crew Competency
A cohesive team is the backbone of a safe engine room. Crew members must collaborate, share knowledge, and support one another to achieve common goals. Regular training ensures that all personnel are equipped with the skills and certifications required by the Standards of Training, Certification, and Watchkeeping (STCW) Convention.
Training programs should cover:
- Engine maintenance and troubleshooting
- Fuel management and bunkering procedures
- Emergency response protocols
- Use of personal protective equipment (PPE)
Certifications, such as those for handling hazardous materials or operating specific machinery, ensure compliance with international standards and enhance crew competency.
3. Defined Procedures and Standing Orders
Well-defined procedures provide a roadmap for safe and efficient operations. The Chief Engineer’s standing orders outline specific protocols for watchkeeping, maintenance, and emergency response. These procedures should be documented in the SMS and communicated to all crew members.
Key procedures include:
- Routine machinery inspections
- Emergency shutdown protocols
- Firefighting and evacuation drills
- Fuel and waste management guidelines
4. Monitoring and Supervision
Continuous monitoring of engine room systems is essential for detecting anomalies and preventing failures. Automated systems, such as engine control panels and condition-based monitoring tools, provide real-time data on parameters like temperature, pressure, and vibration. Supervisors must ensure that these systems are functioning correctly and that crew members respond promptly to alerts.
5. Maintenance and Preventive Measures
Regular maintenance is critical for preventing equipment failures and ensuring safe operations. A Planned Maintenance System (PMS) schedules routine inspections and repairs, while predictive maintenance tools, such as vibration analysis and thermography, identify potential issues before they escalate.
Key maintenance tasks include:
- Filter Replacements: Regularly replace air, fuel, and oil filters to maintain engine performance.
- Connection Inspections: Check hoses, wires, and clamps for wear and tear.
- Pipe Maintenance: Lag steam, fuel, and exhaust pipes to prevent overheating and fires. Inspect pipe supports to minimize vibrations and shock loads.
- Insulation Checks: Survey insulation near oil and fuel systems to prevent leaks.
- Emergency System Testing: Test water piping systems, including emergency nozzles, to ensure functionality during fires.
6. Fire Prevention and Safety
Fire is one of the most significant risks in the engine room, with fuel leaks and oily waste being common causes. According to marine safety reports, approximately 50% of vessel fires originate from pressurized pipe leaks in the engine room. Implementing fire prevention measures is a top priority.
Fire Safety Best Practices
- Oil Disposal Policy: Dispose of oil-contaminated materials, such as rags and filters, in designated containers. Use onboard incinerators or transfer waste to land-based facilities for compliant disposal.
- Fuel Leak Detection: Conduct pressure and tightness tests on fuel pipes to identify leaks. Monitor sensors and gauges for real-time alerts.
- Pipe Maintenance: Minimize joint structures on pipes carrying flammable substances and shield them from hot surfaces. Regularly inspect insulation and supports.
- Firefighting Systems: Maintain CO2 extinguishers, water-mist installations, and emergency nozzles. Conduct regular fire drills to ensure crew readiness.
Fire Risk Assessment Table
Risk Factor | Potential Hazard | Mitigation Strategy |
---|---|---|
Fuel Leaks | Fire outbreak | Conduct pressure/tightness tests, monitor sensors |
Oily Waste | Spontaneous combustion | Use designated disposal containers, incinerate |
Poor Insulation | Overheating, fire | Inspect and lag pipes, shield from hot surfaces |
Faulty Firefighting Systems | Inability to control fires | Test and maintain CO2 and water-mist systems |
7. Bilge Management and Waste Disposal
Proper management of bilge water and waste materials is essential for safety and environmental compliance. Engine room bilges accumulate oil, hydraulic fluid, and other contaminants, which must be separated using an Oily Water Separator (OWS).
Bilge Management Best Practices
- Optimize OWS: Regularly service and clean the OWS to ensure effective separation of oil and water.
- Paint Bilges: Use bright-colored paint to spot leaks easily.
- Drip Trays: Install trays to contain leaks and prevent contamination of other systems.
- Chemical Separation: Store chemical and solvent waste separately to avoid pH imbalances.
- Cleaning Protocols: Use air-powered pressure washers with compatible cleaning agents to sanitize bilge wells. Avoid power washing electrical components, sensors, or deck plates.
Waste Disposal Guidelines
- Sewage and Liquid Waste: Store in retention tanks and dispose of via shore servicing.
- Solid Waste: Store in stainless steel tanks and transfer to land-based facilities.
- Oil-Contaminated Materials: Incinerate onboard or transfer to designated disposal facilities.
8. Environmental Compliance
Compliance with IMO MARPOL Annex VI is mandatory for managing emissions and waste. Key measures include:
- Adhering to fuel quality standards (ISO 8217)
- Implementing emission reduction strategies, such as slow steaming and exhaust scrubbers
- Following Energy Efficiency Operational Indicator (EEOI) guidelines
Non-compliance can result in port detentions and hefty fines, making environmental management a critical component of engine room safety.
Creating a Safety Management System (SMS)
An SMS is a documented framework that outlines safety procedures, roles, and responsibilities. It ensures that all crew members understand their duties and can respond effectively to emergencies.
Key Elements of an SMS
- Personal Protective Equipment (PPE): Mandate anti-slip shoes, helmets, gloves, eyewear, and coveralls.
- Emergency Procedures: Define roles for fire, flooding, and blackout scenarios.
- Safe Working Loads: Specify capacities for lifts and machinery.
- Accident Documentation: Establish protocols for reporting and investigating incidents.
- Electrical Safety: Monitor circuit capacities to prevent overloading.
- Communication Workflows: Ensure clear channels between ship and shore personnel.
- Environmental Policies: Align with flag state regulations for waste and emissions.
SMS Implementation
- Distribute SMS booklets to all crew members.
- Conduct formal training sessions to review procedures.
- Perform regular audits to ensure compliance.
SMS Workflow (Chart)
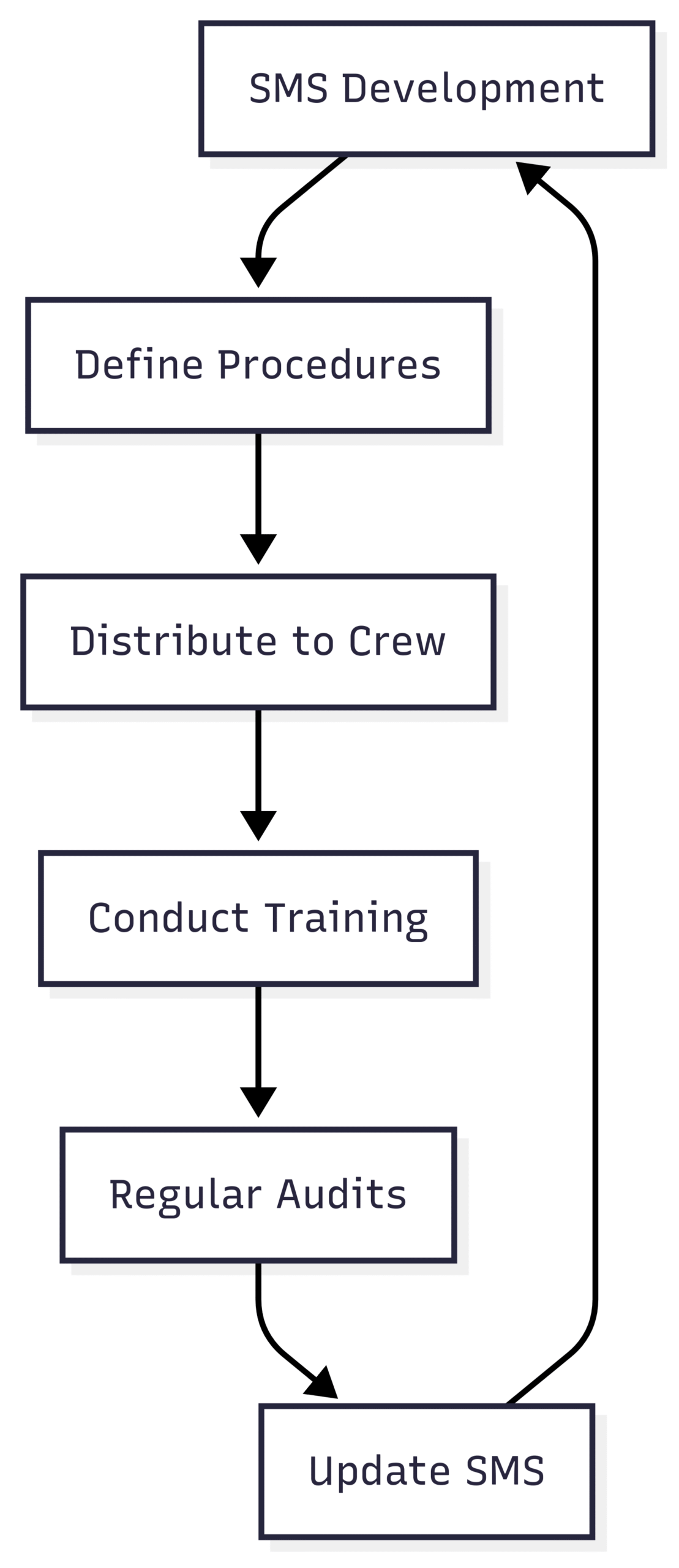
Real-World Case Studies
Case Study 1: Preventing an Engine Room Fire
A bulk carrier experienced a minor fuel leak in the engine room. Thanks to regular pressure tests and sensor monitoring, the crew detected the issue early. Prompt action, including isolating the leak and using firefighting systems, prevented a potential fire. This incident underscores the importance of proactive maintenance and monitoring.
Case Study 2: Efficient Bilge Management
A container ship implemented a robust bilge management system, including frequent OWS servicing and bright-colored bilge paint. During a port inspection, the vessel passed with flying colors, avoiding detention and demonstrating compliance with MARPOL regulations.
Future Trends in Engine Room Safety
Technological advancements are transforming engine room operations, enhancing safety and efficiency.
- Automation and AI: AI-driven systems enable predictive maintenance and real-time decision support.
- Remote Monitoring: Shore-based control centers can monitor engine performance, reducing onboard workload.
- Hybrid Power Systems: LNG, hydrogen, and battery storage systems support greener operations.
- Digital Twins: Virtual models of engine room systems allow for simulations and predictive analytics.
These innovations reduce human error, improve response times, and align with the maritime industry’s push for sustainability.
Conclusion
Safe working practices in the engine room are essential for protecting crew members, optimizing vessel performance, and ensuring compliance with international regulations. By implementing a robust SMS, prioritizing maintenance, and embracing technological advancements, ship operators can create a safe and efficient engine room environment. From fire prevention to bilge management, every aspect of engine room operations requires diligence, teamwork, and adherence to best practices. With these strategies in place, vessels can navigate the seas safely, efficiently, and sustainably.
Happy Boating!
Share Safe Working Practices in the Engine Room with your friends and leave a comment below with your thoughts.
Read Hybrid/dual fuel propulsion systems towards decarbonization until we meet in the next article.