Procedure for Entering an Enclosed Space on a Ship
Learn the essential safety procedures for entering enclosed spaces on ships, including permits, ventilation, and rescue protocols to ensure crew safety.
Enclosed spaces on ships, such as cargo holds, fuel tanks, and cofferdams, pose significant risks due to their confined nature, limited ventilation, and potential for hazardous atmospheres. These spaces are not designed for continuous human occupancy and can harbor toxic gases, flammable vapors, or oxygen-deficient conditions. Entering such spaces without proper precautions can lead to severe injury or death. This article provides a detailed, step-by-step guide to the safety procedures required for entering enclosed spaces on ships, emphasizing risk assessment, preparation, and emergency protocols to ensure crew safety. By adhering to these guidelines, seafarers can mitigate risks and maintain a safe working environment.
What Are Enclosed Spaces?
Enclosed spaces on ships are areas not intended for daily operations or continuous occupancy. They are characterized by:
- Limited Openings: Small entry and exit points that restrict access and egress.
- Inadequate Ventilation: Lack of natural or mechanical airflow, leading to potential accumulation of hazardous gases.
- Non-Designed for Occupancy: Spaces not built for prolonged human presence, often used for storage or machinery housing.
Common examples include:
- Cargo holds
- Fuel and ballast tanks
- Double bottom tanks
- Cofferdams
- Duct keels
- Chain lockers
- Void spaces
- Engine crankcases
- Exhaust and scavenge receivers
A ship-specific list of enclosed spaces should be maintained and displayed prominently to ensure crew awareness. Any space left unventilated for an extended period or affected by environmental changes (e.g., migration of hazardous vapors) must be treated as potentially dangerous.
Dangers of Enclosed Spaces
Enclosed spaces present multiple hazards that can endanger crew members. Understanding these risks is critical for safe entry.
1. Oxygen Deficiency
The acceptable oxygen range for safe entry is 19.5% to 23.5% by volume. Oxygen levels can drop due to:
- Rusting: Oxidation of steel consumes oxygen.
- Hot Work: Welding or cutting reduces oxygen through combustion.
- Inert Gases: Used to prevent explosions, these gases displace oxygen.
- Cargo Residues: Materials like coal or iron ore absorb oxygen over time.
2. Toxic Vapors
Toxic gases, such as carbon monoxide (CO) or hydrogen sulfide (H₂S), can accumulate in enclosed spaces. Even low concentrations (2–5 ppm of H₂S) can cause symptoms like headaches, nausea, or eye irritation. Higher levels can lead to unconsciousness or death.
3. Flammable Gases
Flammable vapors from fuel or chemical residues pose explosion risks, especially during hot work.
4. Restricted Space
Limited space complicates movement and rescue efforts, increasing the risk of entrapment or injury.
5. Poor Lighting
Inadequate illumination heightens the risk of slips, trips, and falls.
6. Leakage from Adjacent Spaces
Hazardous materials from nearby compartments can migrate, introducing unexpected dangers.
7. Lack of Ventilation
Without proper airflow, toxic gases or oxygen-deficient conditions can persist, making the space lethal.
Common Causes of Incidents
Despite safety protocols, accidents in enclosed spaces remain a concern in the maritime industry. Key issues include:
- Failure to recognize hazardous spaces.
- Inadequate training or awareness of onboard hazards.
- Non-compliance with safety procedures or treating checklists as routine.
- Incorrect use of safety equipment.
- Impulsive rescue attempts driven by emotion rather than training.
- Lack of effective communication or supervision.
To address these risks, a structured procedure for enclosed space entry is essential.
Procedure for Safe Enclosed Space Entry
The following steps outline a comprehensive procedure for safely entering enclosed spaces on ships. Each step is designed to minimize risks and ensure crew safety.
1. Risk Assessment
A competent officer must conduct a thorough risk assessment before entry. This involves:
- Identifying Hazards: Assess potential risks, such as toxic gases, oxygen deficiency, or flammable vapors.
- Control Measures: Determine mitigation strategies, such as ventilation or PPE.
- Work Scope: Define the tasks (e.g., welding, cleaning, or inspection) to streamline the assessment process.
- Alternatives: Explore safer methods to achieve the objective without entry, if possible.
Chart: Risk Assessment Process

2. Obtain a Permit to Work
A permit-to-work system is mandatory for enclosed space entry. The permit specifies:
- Location: The specific enclosed space.
- Work Nature: Tasks to be performed and their limitations.
- Team Details: Personnel involved and tools required.
- Hazards: Identified risks from the assessment.
- Precautions: Ventilation, PPE, and communication protocols.
- Validity: Time period for which the permit is valid (typically 8–24 hours).
- Signatures: Authorization from the Master or designated officer and confirmation from the entrant.
The permit must be reissued if the validity period expires or conditions change.
3. Ventilation
Proper ventilation is critical to ensure a safe atmosphere. Steps include:
- Natural or Mechanical Ventilation: Use blowers or open hatches to introduce fresh air.
- Sufficient Time: Allow enough time for air circulation to stabilize oxygen levels.
- Continuous Ventilation: Maintain airflow during entry to prevent gas accumulation.
4. Atmosphere Testing
Use calibrated gas detectors to measure:
- Oxygen Levels: Must be 20% by volume (19.5–23.5% acceptable).
- Toxic Gases: Check for carbon monoxide, hydrogen sulfide, and other hazardous vapors.
- Flammable Gases: Ensure no risk of explosion.
Testing should be conducted at multiple levels (top, middle, bottom) and through all available openings to obtain a representative sample. The table below summarizes gas behavior:
Gas | Behavior | Health Effects |
---|---|---|
Methane (CH₄) | Rises (lighter than air) | Asphyxiation risk |
Carbon Monoxide (CO) | Stays in middle (similar to air) | Headache, unconsciousness, death |
Carbon Dioxide (CO₂) | Sinks (heavier than air) | Asphyxiation, dizziness |
Hydrogen Sulfide (H₂S) | Sinks (heavier than air) | Eye irritation, nausea, death |
5. Personal Protective Equipment (PPE)
Entrants must wear appropriate PPE based on the risk assessment, including:
- Breathing Apparatus: Self-contained breathing apparatus (SCBA) for oxygen-deficient or toxic environments.
- Protective Clothing: Flame-resistant suits, gloves, and boots.
- Helmets and Harnesses: For fall protection and rescue purposes.
6. Communication Systems
Establish reliable communication between the entrant and standby personnel. Options include:
- Two-Way Radios: Tested before entry.
- Lifelines: Physical connection for signaling in case of radio failure.
- Agreed Intervals: Regular check-ins to confirm safety.
7. Standby Personnel
A designated standby person must remain at the entrance to:
- Monitor the entrant’s condition.
- Maintain communication with the officer of the watch.
- Initiate rescue procedures if needed.
8. Rescue and Emergency Preparedness
Rescue procedures must be planned and rehearsed, with equipment readily available:
- Rescue Equipment: Breathing apparatus, stretchers, tripods, and hoisting gear.
- Trained Team: Crew members trained in confined space rescue.
- Emergency Protocols: Clear steps to activate the ship’s emergency response system.
Chart: Rescue Procedure
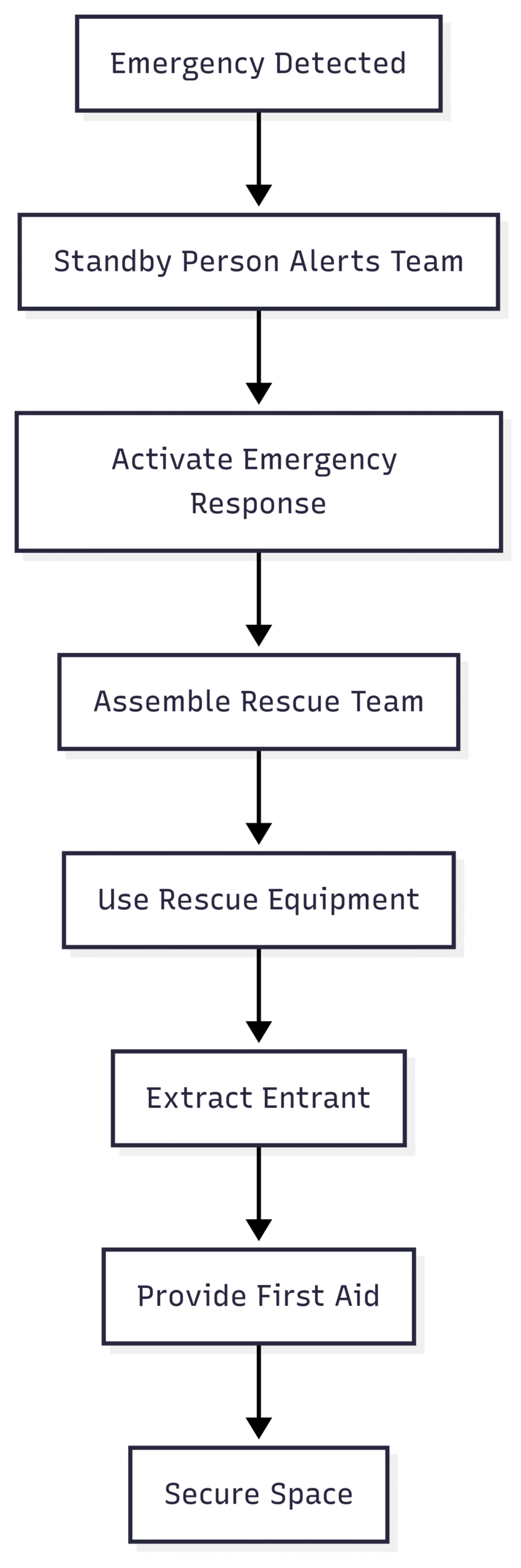
9. Post-Entry Procedures
After completing work:
- Evacuate the Space: Ensure all personnel exit safely.
- Close the Permit: Verify completion with signatures from the entrant and officer.
- After-Work Checklist: Confirm the space is secure and equipment is removed.
- Debrief: Evaluate the operation to identify improvements.
Importance of Enclosed Space Drills
Regular drills are critical for maintaining proficiency in enclosed space entry and rescue procedures. Since January 2015, drills have been mandatory every two months. Benefits include:
- Familiarity: Crew members gain hands-on experience with safety protocols.
- Confidence: Builds ability to handle real emergencies.
- Equipment Testing: Ensures rescue gear is functional.
- Feedback: Post-drill evaluations identify gaps and improve procedures.
Drills should simulate realistic scenarios, involve all crew members, and encourage open communication to address concerns.
Best Practices for Safe Entry
To enhance safety, consider the following:
- Never Enter Alone: Always have a standby person and proper authorization.
- Treat All Spaces as Hazardous: Assume danger until proven safe through testing.
- Avoid Impulsive Actions: Follow training, not emotions, during emergencies.
- Supervise New Crew: Provide coaching to ensure understanding of risks.
- Use Signage: Display “Men at Work” signs to prevent accidental equipment activation.
Case Studies: Lessons from Incidents
Case Study 1: Oxygen Deficiency in Cargo Hold
A seafarer entered a cargo hold without proper ventilation, assuming it was safe due to recent use. The oxygen level was below 19.5% due to rusting, leading to unconsciousness. The standby person initiated a rescue, but the delay in emergency response caused severe injury. Lesson: Always test the atmosphere and ensure continuous ventilation.
Case Study 2: Toxic Gas Exposure
During tank cleaning, a crew member inhaled hydrogen sulfide from residual cargo, resulting in collapse. The rescue team entered without PPE, leading to multiple casualties. Lesson: Proper PPE and planned rescue procedures are non-negotiable.
Safety Equipment Specifications and Costs
The table below outlines common equipment used for enclosed space entry, including specifications and approximate costs (based on standard maritime suppliers):
Equipment | Specifications | Approx. Cost (USD) |
---|---|---|
Gas Detector | Multi-gas (O₂, CO, H₂S, CH₄), portable | $500–$1,500 |
Self-Contained Breathing Apparatus (SCBA) | 30-minute air supply, 6.8L cylinder | $2,000–$4,000 |
Rescue Tripod | Aluminum, 2.4m height, 500kg capacity | $800–$1,200 |
Two-Way Radio | Waterproof, 5W, 10km range | $100–$300 per unit |
Protective Suit | Flame-resistant, chemical-resistant | $200–$500 |
Note: Prices vary based on brand, region, and supplier. For precise costs, contact maritime safety equipment providers.
Regulatory Framework
Enclosed space entry is governed by international regulations, including:
- SOLAS Chapter XI-1: Mandates safety procedures for confined spaces.
- IMO Resolution A.1050(27): Provides guidelines for safe entry and rescue.
- OSHA Standards: Define enclosed spaces and safety requirements for maritime operations.
Compliance with these regulations ensures legal adherence and enhances crew safety.
Conclusion
Entering enclosed spaces on ships is a high-risk activity that demands strict adherence to safety procedures. By conducting thorough risk assessments, obtaining permits, ensuring proper ventilation, testing atmospheres, and preparing for emergencies, seafarers can significantly reduce risks. Regular drills and robust training further enhance preparedness, while lessons from past incidents underscore the importance of compliance. By prioritizing safety and following established protocols, the maritime industry can prevent accidents and protect lives in these hazardous environments.
Happy Boating!
Share Procedure for Entering an Enclosed Space on a Ship with your friends and leave a comment below with your thoughts.
Read Risk Assessment for Ships: A General Overview until we meet in the next article.