LNG Bunkering Procedure Of Ships Explained
Discover the detailed LNG bunkering procedure for ships, ensuring safe fuel transfer with preparation, transfer, and post-bunkering steps.
Liquefied Natural Gas (LNG) is transforming the maritime industry as a cleaner alternative to conventional heavy fuel oil and low-sulfur fuel oil (LSFO). With stringent sulfur regulations, such as those enforced by the International Maritime Organization (IMO) in 2020, LNG has become a preferred fuel for ships aiming to reduce harmful emissions. However, bunkering LNG—a cryogenic fuel stored at -162°C—requires a meticulous and highly regulated procedure to ensure safety, efficiency, and environmental protection. This article provides an in-depth exploration of the LNG bunkering process for ships, covering preparation, transfer, post-bunkering activities, specific considerations, and associated hazards.
Understanding LNG Bunkering
LNG bunkering involves transferring liquefied natural gas from a supplier (bunker vessel, truck, or shore-based terminal) to a receiving vessel, such as a cruise or container ship equipped with dual-fuel engines. Unlike traditional fuel oils, LNG’s cryogenic nature and potential for boil-off gas (BOG) necessitate specialized equipment, rigorous safety protocols, and compliance with international regulations, including the IMO’s International Code of Safety for Ships using Gases or other Low-flashpoint Fuels (IGF Code) and the International Code for the Construction and Equipment of Ships Carrying Liquefied Gases in Bulk (IGC Code).
The process is complex due to LNG’s unique properties, such as its low temperature, potential for vaporization, and associated hazards like cryogenic burns, fire risks, and oxygen depletion. Effective LNG bunkering requires precise coordination between the supplier and receiving vessel, comprehensive crew training, and robust safety measures to mitigate risks.
The LNG Bunkering Procedure
The LNG bunkering process is divided into three main phases: preparation, transfer, and post-bunkering. Each phase involves specific steps to ensure a safe and efficient operation.
1. Preparation Phase
The preparation phase is critical to establishing a safe and controlled environment for LNG bunkering. This phase involves planning, equipment checks, safety measures, and tank preparation.
Planning and Communication
A detailed bunkering plan is developed, specifying the tanks to be filled, the quantity of LNG required, and the transfer rate. The receiving vessel’s master and the supplier’s representative agree on key parameters, including maximum loading rates, communication protocols, and emergency procedures. Both parties sign off on pre-bunkering checklists to confirm readiness.
Clear communication channels are established, typically via VHF radio or other dedicated systems, to ensure real-time coordination during the operation. For ship-to-ship bunkering, mooring arrangements are finalized, and both vessels confirm the compatibility of their bunker pipe flanges and vapor return lines (if applicable).
Equipment Readiness
All bunkering equipment, including hoses, couplings, and safety devices, is inspected for compatibility and functionality. LNG bunkering often employs Quick Connect/Disconnect Couplings (QCDC), which are dry-break couplings designed to form a liquid- and pressure-tight seal. These couplings feature a valve arrangement that halts liquid flow before disconnection, preventing spills. QCDC systems support flow rates up to 650 m³/h with a maximum velocity of 10 m/s for nominal sizes up to 6 inches.
Hoses are color-coded per industry standards to prevent the use of incorrect hose types. The bunker pipe and vapor return line (if provided) are secured, and electrical grounding is ensured to avoid arcing during connection.
Safety Measures
Safety is paramount in LNG bunkering due to the fuel’s cryogenic and flammable properties. Spill containment equipment, such as absorbent materials and drip trays, is placed near the bunkering station. Fire-fighting equipment, including dry powder extinguishers and foam monitors, is checked and positioned for immediate use. Warning signs are posted around the bunkering area, designating it as an EX-classified (explosion-hazard) zone during the operation.
Crew members involved in bunkering wear specialized personal protective equipment (PPE), including:
- Cryogenic gloves to protect against frostbite and burns.
- Tightly fitting safety goggles and face shields with side protection.
- Flame-resistant, cryogenic-retardant clothing with high-visibility markings covering the entire body.
An Emergency Shutdown (ESD) system is tested on both the receiving vessel and the supplier to ensure rapid cessation of fuel flow in case of emergencies, such as leaks, power loss, or worsening weather conditions.
Tank Preparation
The receiving vessel’s tanks are prepared by measuring ullage (available space) to confirm sufficient capacity. High-level alarms are tested to prevent overfilling. Tank temperatures and pressures are checked to ensure they are within safe limits, as variations can lead to vaporization and pressure spikes during bunkering. If a vapor return line is not used, the receiving vessel must have a Boil-Off Gas Management system or the ability to handle vapor pressure without generating excessive BOG.
Weather and Timing Considerations
The master of the receiving vessel reviews weather and tide forecasts to ensure safe conditions for bunkering. Operations are preferably conducted during daylight to enhance visibility and safety. Adverse weather, such as high winds or rough seas, may necessitate postponing the operation.
2. Transfer Phase
The transfer phase involves the actual delivery of LNG from the supplier to the receiving vessel. This phase requires continuous monitoring and precise control to prevent spills, overfilling, or equipment failure.
Slow Start
The transfer begins at a low pumping rate to check for leaks and ensure proper flow into the designated tanks. Crew members monitor the bunker station and manifold for signs of irregularities, such as loose connections or pressure anomalies.
Monitoring and Rate Adjustments
Both the supplier and receiving vessel continuously monitor tank levels, flow rates, and pressures. Electronic tank gauging systems are cross-checked with manual soundings to ensure accuracy. The transfer rate, which depends on whether top-spray or bottom-flow filling is used, is adjusted as needed to stay within agreed limits. The supplier notifies the receiving vessel before making any rate changes.
Tank Switching
When switching between tanks, the flow is carefully managed to avoid overfilling. High-level alarms provide an additional layer of protection, triggering an immediate shutdown via the ESD system if necessary.
Sampling
Representative LNG samples are collected during the transfer for quality control and regulatory compliance. These samples are sealed, labeled, and distributed as follows:
- One portion is retained onboard the receiving vessel.
- One portion is given to the supplier.
- One portion is sent for laboratory analysis.
Safety Zone Monitoring
Only authorized personnel are allowed in the safety zone around the bunkering station. The crew continuously monitors mooring lines, security zones, and environmental conditions to ensure the operation remains safe.
Emergency Protocols
If any issues arise—such as leaks, loose mooring lines, power loss, or communication failures—the bunkering operation is halted immediately. The ESD system can be activated manually or automatically to stop the fuel flow. Crew members are trained to respond swiftly to hazards, using communication channels or the ESD switch as appropriate.
3. Post-Bunkering Phase
The post-bunkering phase ensures the operation is completed safely, equipment is stowed, and documentation is finalized.
Final Soundings
After the agreed quantity of LNG is delivered, final tank soundings are taken to verify the received amount. This step confirms that the transfer matches the Bunker Delivery Note (BDN).
Hose Disconnection
The bunker hose and vapor return line (if used) are drained and inerted to remove residual LNG. The QCDC system ensures a dry disconnection, minimizing the risk of spills. The hose is then disconnected and returned to the supplier.
Documentation
All bunkering activities are recorded in the vessel’s logbooks and the BDN. The BDN includes details such as the quantity delivered, transfer rates, and sample information. The chief engineer of the receiving vessel signs the BDN to confirm receipt.
Sample Management
LNG samples are properly sealed and labeled for storage or analysis. This ensures compliance with regulatory requirements and facilitates quality verification.
Clean-Up
The bunkering area is cleaned, and all equipment, including spill containment materials and fire-fighting gear, is stowed. The manifold is blanked to prevent contamination.
Specific Considerations for LNG Bunkering
LNG bunkering presents unique challenges due to its cryogenic nature and potential hazards. Key considerations include:
Low Temperatures
LNG is stored and transferred at -162°C, requiring specialized equipment to prevent brittle fracture and manage boil-off gas. Hoses, couplings, and tanks are designed to withstand extreme cold, and crew members must be protected from cryogenic burns.
Vapor Management
Boil-off gas is managed through vapor return lines or onboard BOG management systems. The receiving vessel must control vapor pressure to prevent tank overpressurization. If no vapor return line is provided, the vessel must have mechanisms to cool LNG or handle BOG without generating excessive vapors.
Emergency Shutdown Systems
ESD systems are critical for halting fuel flow in emergencies. They are triggered by conditions such as:
- Detection of leaks or spills.
- Loss of power or communication.
- Loose mooring lines.
- Worsening weather or sea conditions.
Regulatory Compliance
LNG bunkering operations must adhere to:
- IMO IGC Code: Governs the design and operation of bunker vessels carrying LNG.
- IMO IGF Code: Provides interim guidelines for ships receiving LNG as fuel.
- Local port authority regulations, which may require permits and specific procedures.
Hazards Associated with LNG Bunkering
LNG bunkering introduces several hazards that must be mitigated through careful planning and execution. These include:
Hazard | Description | Mitigation Measures |
---|---|---|
Leaks and Spills | Loose connections or ruptured hoses can lead to LNG spills. | Regular inspection of hoses and couplings, use of spill containment equipment, and activation of ESD systems. |
Cryogenic Burns | Contact with LNG at -162°C can cause frostbite or burns. | Use of cryogenic PPE, including gloves and face shields. |
Flash Fire | Ignition of LNG vapor in an open area without pressure buildup. | Monitoring of flammable gas concentrations and use of EX-classified zones. |
Jet Fire | High-pressure LNG release ignites, causing structural damage. | Pressure monitoring and robust equipment design. |
Pool Fire | Spilled LNG evaporates and ignites on land or water. | Spill containment and rapid response with fire-fighting equipment. |
BLEVE | Boiling Liquid Expanding Vapor Explosion from heated LNG in a closed tank. | Temperature and pressure monitoring, robust tank design. |
Rapid Phase Transition (RPT) | Sudden vaporization due to heat transfer. | Controlled transfer rates and temperature management. |
Bunker Line Contamination | Ice formation from moisture or CO2 in bunker lines. | Inerting lines before and after bunkering. |
Trapped LNG | Residual LNG in pipes expands into vapor, causing pressure buildup. | Proper draining and inerting of lines. |
Rollover | Rapid release of LNG vapors due to stratification in tanks. | Monitoring tank temperature and density gradients. |
Oxygen Deficiency | LNG vaporization in confined spaces displaces oxygen. | Ventilation and gas detection systems in enclosed areas. |
Chart: LNG Bunkering Hazard Mitigation Workflow
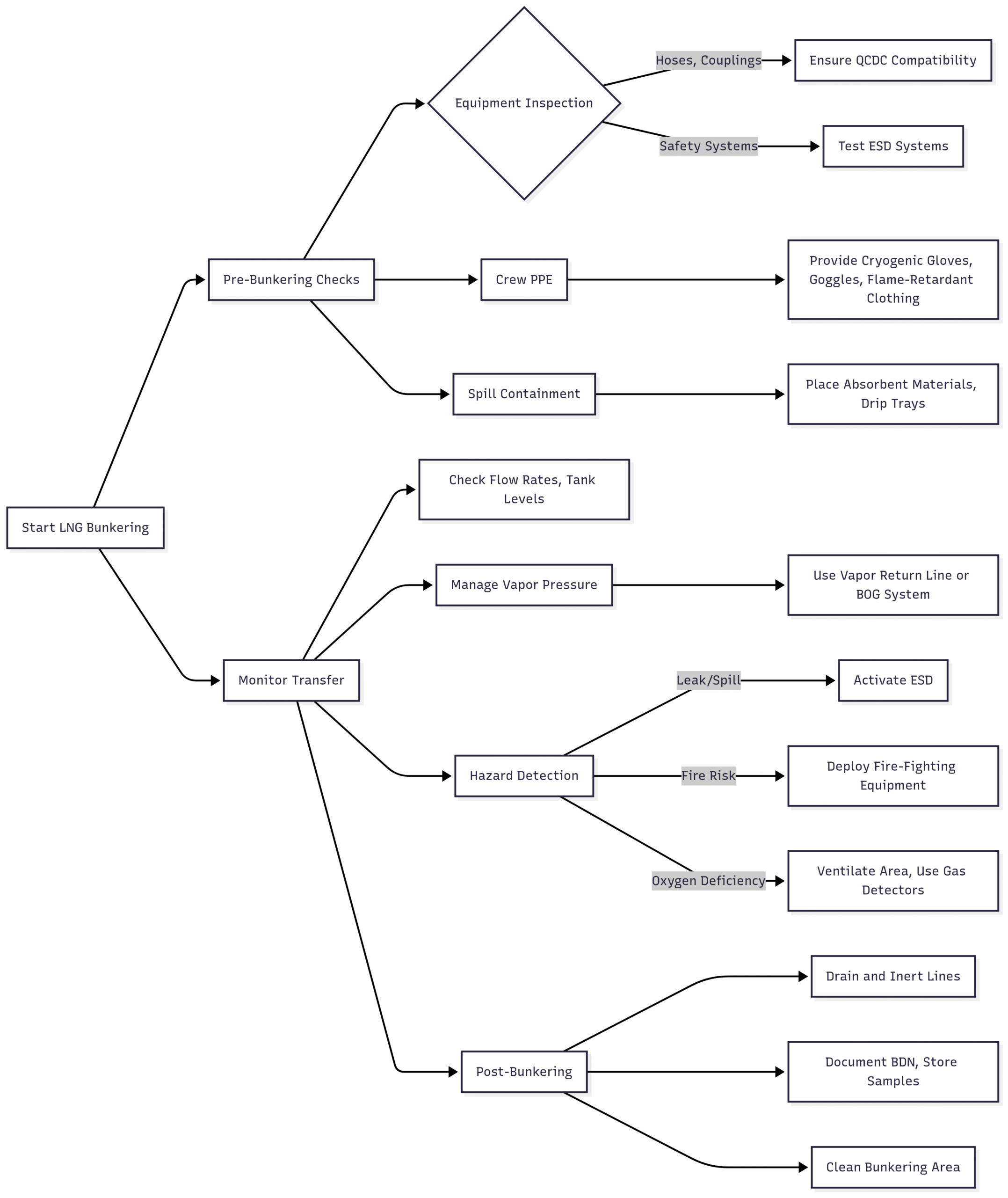
Crew Training and Responsibilities
Effective LNG bunkering relies on well-trained crew members who understand the procedure and associated hazards. Training programs should cover:
- LNG properties and safety risks.
- Operation of QCDC couplings and ESD systems.
- Emergency response protocols for spills, fires, and oxygen depletion.
- Use of specialized PPE.
Checklists outlining each crew member’s responsibilities during bunkering are displayed prominently and reviewed regularly. The master and chief engineer oversee the operation, ensuring compliance with regulations and coordination with the supplier.
Equipment Specifications
Equipment | Specification | Purpose |
---|---|---|
QCDC Coupling | Nominal size up to 6 inches, flow rate up to 650 m³/h, max velocity 10 m/s | Ensures liquid- and pressure-tight connection, enables quick connect/disconnect. |
Cryogenic Hoses | Color-coded, designed for -162°C | Transfers LNG safely, prevents incorrect hose use. |
Vapor Return Line | Optional, depends on vessel’s BOG management | Manages boil-off gas to prevent tank overpressurization. |
ESD System | Automated or manual activation | Halts fuel flow in emergencies. |
Spill Containment | Absorbent materials, drip trays | Mitigates environmental impact of spills. |
Environmental and Regulatory Context
The adoption of LNG as a marine fuel aligns with global efforts to reduce shipping emissions. The IMO’s 2020 sulfur cap (0.5% sulfur content) has driven the use of LNG, which produces negligible sulfur oxides (SOx) and reduced nitrogen oxides (NOx) and particulate matter compared to traditional fuels. Compliance with the IMO IGF and IGC Codes ensures that LNG bunkering meets international safety and environmental standards. Local port regulations may impose additional requirements, such as permits or restrictions on bunkering locations.
Challenges and Future Outlook
While LNG bunkering offers environmental benefits, challenges remain, including:
- Infrastructure Development: Expanding LNG bunkering facilities at ports.
- Cost: Initial investment in LNG-compatible vessels and equipment is high, though long-term fuel savings may offset costs.
- Standardization: Harmonizing bunkering procedures and equipment across ports.
As the maritime industry transitions to cleaner fuels, LNG bunkering is expected to grow, supported by advancements in technology and infrastructure. Innovations in BOG management, cryogenic equipment, and safety systems will further enhance the efficiency and safety of LNG bunkering.
Conclusion
LNG bunkering is a complex but essential process for enabling cleaner maritime operations. By adhering to rigorous preparation, transfer, and post-bunkering procedures, ships can safely and efficiently receive LNG fuel. The use of specialized equipment, comprehensive crew training, and strict regulatory compliance ensures that bunkering operations minimize risks and protect the environment. As the industry continues to embrace LNG, standardized procedures and ongoing innovation will solidify its role as a cornerstone of sustainable shipping.
Happy Boating!
Share LNG Bunkering Procedure Of Ships Explained with your friends and leave a comment below with your thoughts.
Read Boat Wheel PNG Images 4K HD Wallpapers until we meet in the next article.