Learn about the critical role of emergency bilge suction valves in ships’ engine rooms, their design, SOLAS compliance, and importance in preventing flooding.
The engine room of a ship is a critical hub, housing the machinery that powers the vessel. However, it is also one of the most vulnerable areas to flooding, which can lead to catastrophic consequences such as equipment damage, loss of stability, or even sinking. The emergency bilge suction valve is a vital safety component designed to address such emergencies by rapidly removing large volumes of water from the engine room. This article provides an in-depth exploration of the emergency bilge suction valve, covering its functionality, design, regulatory requirements, maintenance practices, and real-world applications, offering valuable insights for ship operators, engineers, and maritime enthusiasts.
What is an Emergency Bilge Suction Valve?
An emergency bilge suction valve is a specialized component of a ship’s bilge system, engineered to remove significant amounts of water from the engine room during emergencies such as flooding caused by hull breaches, grounding, or collisions. Unlike standard bilge pumps used for routine dewatering, this valve is reserved for critical situations, connecting to high-capacity pumps to discharge water overboard, thereby preventing severe damage and ensuring the vessel’s safety.
Key Features
- Emergency Use Only: Reserved for critical flooding scenarios, not for routine bilge dewatering.
- Overboard Discharge: Facilitates the rapid expulsion of water into the sea via the bilge system.
- Location and Accessibility: Positioned in the engine room, often painted red for visibility, and designed for quick access during emergencies.
- Normally Closed: Kept closed during normal operations to prevent accidental discharge or backflooding.
- Regulatory Compliance: Adheres to international standards, such as SOLAS (Safety of Life at Sea), ensuring reliability and safety.
- Maintenance Requirements: Requires regular testing and maintenance to ensure operational readiness.
Importance of Emergency Bilge Suction Valves
The emergency bilge suction valve plays a pivotal role in maintaining ship safety during flooding incidents. Its importance can be summarized in three key areas:
- Rapid Dewatering: In flooding emergencies, the valve enables swift water removal, preventing the engine room from becoming overwhelmed and reducing the risk of sinking.
- Protection of Machinery: By removing water, the valve protects critical equipment such as engines, generators, and electrical systems from water damage.
- Ship Stability: Accumulated water can shift a ship’s center of gravity, compromising stability. The valve mitigates this risk by efficiently expelling water.
A real-world incident underscores its significance: during a severe storm, a tanker experienced flooding when a seabay vent pipe failed. The second engineer activated the emergency bilge suction valve, using a high-capacity pump to discharge water, stabilizing the vessel and preventing further damage.
Design and Operation
Location and Accessibility
The emergency bilge suction valve is strategically located in the engine room, typically on an accessible platform. Its bright red color aids identification during high-stress situations. According to SOLAS Regulation II-1/48.3, the valve’s controls must be positioned to allow sufficient time for operation, even in flooding conditions. In some designs, controls are placed above the flood level to ensure accessibility.
Connection to Pumps
The valve is connected to high-capacity pumps, such as the main cooling water pump or dedicated emergency pumps. For instance, a Jabsco Bronze pump, belt-driven off the engine’s crank pulley, can deliver up to 60 GPM (3,600 GPH). A non-return device is often included to prevent backflow, ensuring water is discharged overboard without re-entering the bilge.
Normally Closed Mechanism
To prevent accidental operation, the valve remains closed during normal conditions. Some ships employ padlocks or numbered seals to secure it, with keys held by senior personnel like the Chief Engineer. This practice, while effective for preventing unauthorized discharges, can delay emergency response if keys are not readily available.
Regulatory Framework
The design and operation of emergency bilge suction valves are governed by SOLAS Chapter II-1, Regulation 35-1 and Regulation 48.3, which outline requirements for bilge pumping arrangements and valve controls in periodically unattended machinery spaces. These regulations ensure that the valve is easily operable and that controls are accessible during flooding. Additionally, IMO MSC.1/Circ.1424 provides unified interpretations, clarifying that the emergency bilge suction valve (referred to as a “bilge injection system” or “direct suction”) must be normally closed and equipped with a non-return device to meet safety standards.
Maintenance and Testing
Regular maintenance and testing are crucial to ensure the valve’s reliability. A Port State Control (PSC) inspection incident highlighted the consequences of neglect: an emergency bilge suction valve was found stuck during a routine test, rendering it inoperable. To prevent such failures, the following practices are recommended:
- Routine Inspections: Conduct frequent tests as per the ship’s Planned Maintenance System (PMS) to verify valve functionality.
- Lubrication: Grease moving parts, such as shaft joints, to prevent sticking.
- Full Operation Checks: Ensure the valve can fully open and close without obstruction.
- Record-Keeping: Maintain detailed records of maintenance and testing activities.
- Crew Training: Provide regular training to ensure crew familiarity with the valve’s operation and emergency protocols.
- Clear Markings: Label valves and controls clearly to prevent accidental operation.
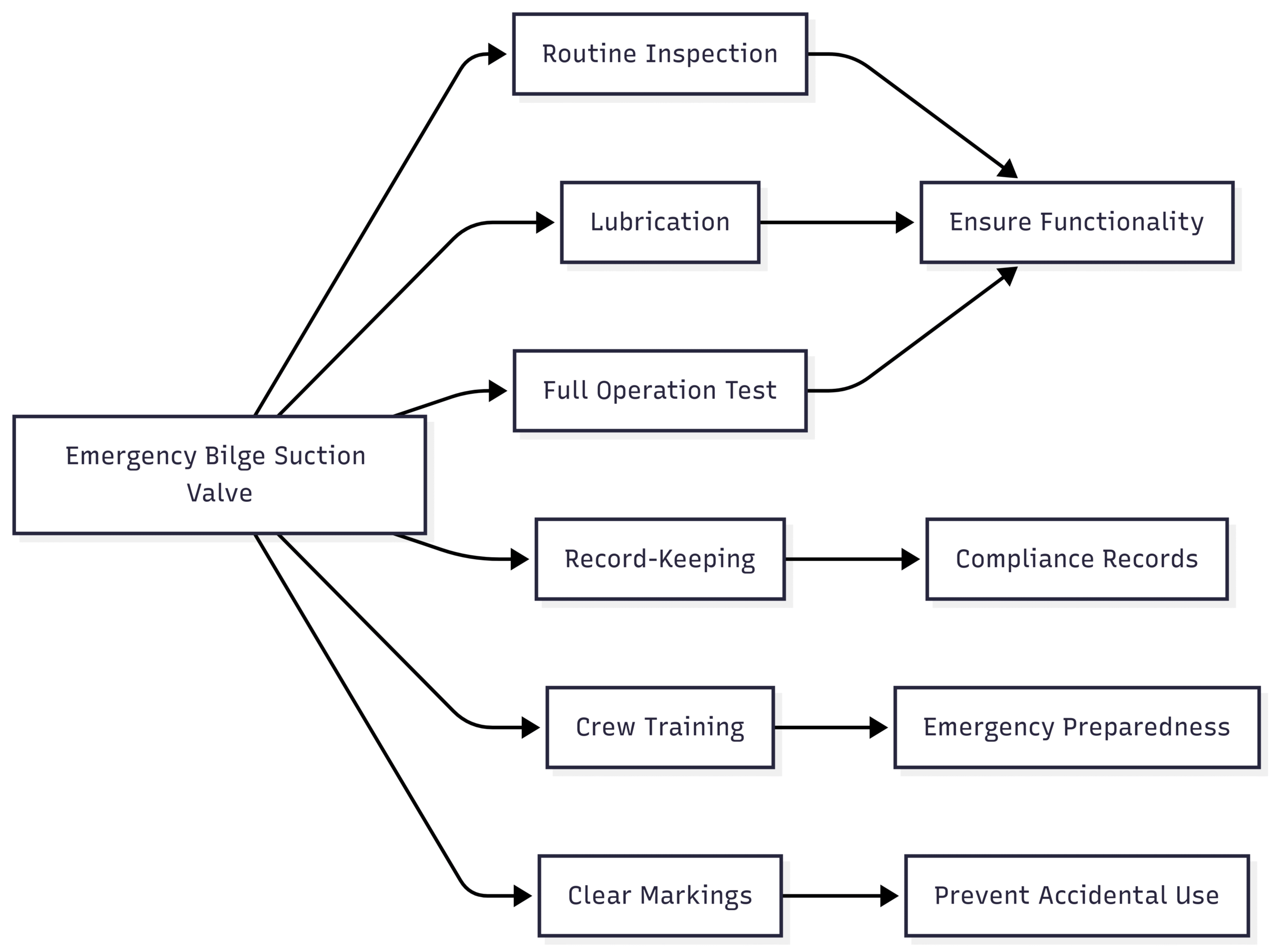
Emergency Pumping Capacity: Insights from the Field
Maritime professionals often discuss the adequacy of emergency pumping systems. For example, a 54-foot yacht owner described their setup: a 2,000 GPH pump in the forward machinery bilge, two 2,000 GPH pumps in the lazarette, and a 3,700 GPH pump in the engine room, all DC-powered. They also carried a small 110V submersible utility pump but sought higher-capacity portable options. Other operators shared similar setups:
- Capt Ralph: Operates a 3,700 GPH 32V pump in the engine room, three 2,000 GPH 32V pumps aft, two 2,000 GPH 32V pumps forward, and a 60 GPM (3,600 GPH) Jabsco Bronze crash pump driven by the starboard engine. A new 24V bus was installed to support larger pumps in the future.
- Pascal: Upgraded a 53-foot motor yacht with four 3,700 GPH pumps with new wiring and high-water alarms. A fifth pump was planned for added safety. Smaller vessels, like a 26-foot day sailor, were equipped with three 1,800 GPH pumps.
- DOCKMASTER: Uses a 3,600 GPH Jabsco pump and considered portable submersible pumps but found them comparable to existing DC pumps.
- motoryachtlover: Employs a Multiquip 2” electric pump capable of 60 GPM (3,600 GPH) at a 15-foot head, using a collapsible hose for easy stowage. This pump is common in excavation and tolerates debris.
Comparative Analysis of Pump Options
Pump Type | Capacity (GPH) | Power Source | Pros | Cons |
---|---|---|---|---|
DC Bilge Pump | 2,000–3,700 | Battery (12V/24V/32V) | Reliable, no generator needed, easy to install | Limited by battery life |
Engine-Driven Pump | Up to 3,600 | Engine | High capacity, independent of electrical system | Requires engine operation, complex installation |
AC Submersible Pump | ~3,600 | Generator (110V/220V) | Portable, debris-tolerant | Dependent on generator, lower capacity |
Gasoline Trash Pump | Up to 18,000 | Gasoline | Very high capacity, portable | Bulky, requires fuel, not ideal for confined spaces |
Key Considerations
- DC vs. AC Pumps: DC pumps are preferred for emergencies due to their independence from generators, which may fail during flooding. For example, Capt Ralph emphasized that a large DC pump can outperform an AC pump in critical situations.
- Engine-Driven Pumps: While powerful, they require manual valve operation in the engine room, posing risks in flooding conditions. Pascal noted the risk of burning out pumps if the bilge runs dry.
- Portable Pumps: High-capacity portable pumps, like gasoline-powered trash pumps (up to 300 GPM or 18,000 GPH), offer significant dewatering potential but are less practical due to size and fuel requirements.
Padlocking and Security Concerns
The practice of padlocking bilge valves to prevent unauthorized discharges, particularly in U.S. territorial waters, has sparked debate. U.S. Coast Guard regulations require bilge overboard valves to be padlocked and logged in the E-Log Book to prevent illegal discharges under MARPOL Annex I. However, padlocking emergency bilge suction valves can delay critical operations during flooding.
A former cadet raised this issue, suggesting a weak-link system with numbered seals to balance security and accessibility. Breaking the seal in an emergency would allow immediate valve operation while maintaining a record of use. Industry feedback includes:
- JollyJack: Emphasized the need for immediate access, stating that a padlocked valve could hinder emergency response, citing a personal experience during a storm where rapid valve operation was critical.
- The Dieselduck: Noted that seals with logbooks are common, with some ships using padlocks and nearby keys. Modern crew incentives to report illegal discharges reduce the need for extreme measures like drilling valve stems.
- Merlyn: Highlighted the increased regulatory burden compared to older practices, where valves were not chained shut.
SOLAS does not explicitly prohibit padlocking but requires bilge pumping equipment to be immediately operable, suggesting that padlocks could contravene regulations if they impede emergency access. Many companies use numbered seals and logbooks to track valve operations, balancing compliance with safety.
Practical Applications and Case Studies
Case Study: Stuck Valve Incident
During a Port State Control inspection, an emergency bilge suction valve was found stuck, highlighting the importance of regular maintenance. The vessel’s Planned Maintenance System (PMS) was updated to include more frequent testing, preventing future failures.
Case Study: Storm-Induced Flooding
A tanker experienced severe flooding during a storm when a seabay vent pipe failed. The emergency bilge suction valve, connected to a high-capacity pump, was activated, discharging water at 60 GPM, stabilizing the ship and preventing machinery damage.
User Experiences
- Capt Ralph’s 32V System: Successfully used a 3,600 GPH crash pump to dewater flooded bilges in minutes, demonstrating the effectiveness of engine-driven pumps in emergencies.
- Pascal’s Upgrades: Enhanced a 53-foot yacht with multiple 3,700 GPH pumps and high-water alarms, emphasizing redundancy and early warning systems.
- motoryachtlover’s Portable Solution: Utilized a Multiquip pump for flexibility, though limited by generator dependency.
Specifications and Pricing
Common Emergency Bilge Pumps
Pump Model | Capacity (GPH) | Power Source | Hose Size | Approx. Price (USD) |
---|---|---|---|---|
Rule 3700 | 3,700 | 12V/24V DC | 1.5”–2” | $200–$300 |
Jabsco Bronze Clutch Pump | 3,600 | Engine-Driven | 2” | $1,000–$1,500 |
Multiquip QP2H | 3,600 | 110V AC | 2” | $500–$700 |
Honda WX15 (Gas Trash Pump) | 14,400 | Gasoline | 3” | $600–$800 |
Valve Specifications
- Material: Bronze or stainless steel for corrosion resistance.
- Size: Typically 2”–4” diameter, depending on pump capacity.
- Type: Gate or ball valve with non-return mechanism.
- Price: $100–$500, depending on size and material.
Installation Costs
- Retrofit Installation: $1,000–$5,000, including labor and piping modifications.
- New Vessel Integration: Included in engine room design, typically $500–$2,000 additional cost.
Best Practices for Implementation
- Redundancy: Install multiple pumps (e.g., 3,700 GPH DC pumps) across different bilge compartments for backup capacity.
- High-Water Alarms: Equip bilges with alarms to alert crew early, as emphasized by Pascal.
- Portable Backup: Carry a portable pump like the Multiquip QP2H for flexibility, ensuring a collapsible hose for easy deployment.
- Seal Systems: Use numbered seals instead of padlocks to balance MARPOL compliance with emergency access.
- Training Drills: Conduct regular flooding simulations to ensure crew proficiency.
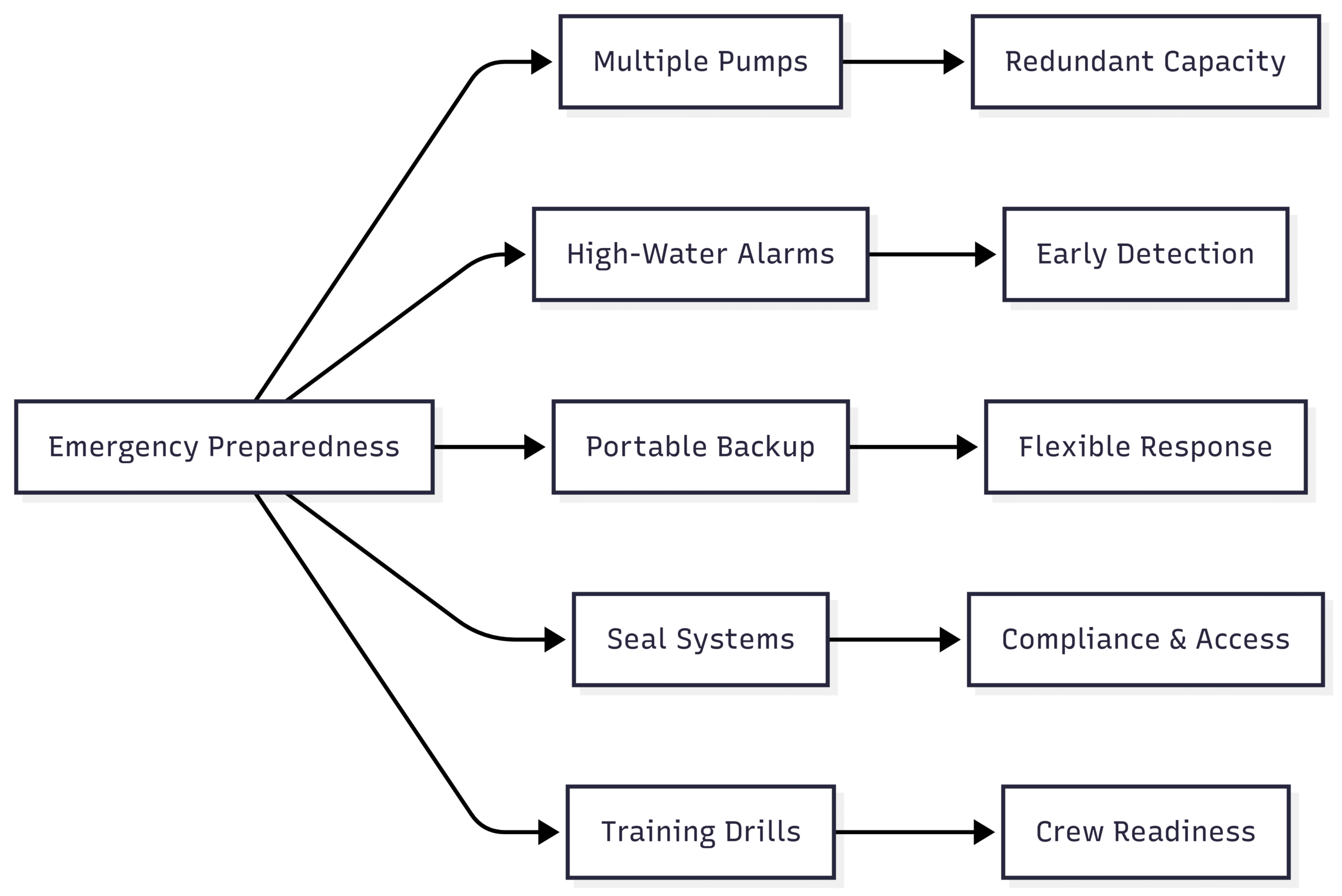
Challenges and Solutions
Challenge: Padlock Delays
Padlocking valves to comply with MARPOL can delay emergency access.
Solution: Use numbered seals with a logbook, allowing quick breaking in emergencies while maintaining compliance.
Challenge: Valve Maintenance
Stuck valves can fail during emergencies.
Solution: Implement a robust PMS with frequent lubrication and testing schedules.
Challenge: Power Dependency
AC pumps rely on generators, which may fail.
Solution: Prioritize DC or engine-driven pumps for reliability.
Challenge: Limited Space
Smaller vessels may lack space for large pumps.
Solution: Opt for compact, high-capacity DC pumps or portable units.
Conclusion
The emergency bilge suction valve is a cornerstone of maritime safety, designed to protect ships from the devastating effects of engine room flooding. By enabling rapid dewatering, protecting machinery, and maintaining stability, this valve is indispensable in emergencies. Compliance with SOLAS and MARPOL regulations, coupled with regular maintenance and crew training, ensures its reliability. Whether using DC pumps, engine-driven systems, or portable solutions, ship operators must prioritize redundancy and accessibility. By understanding and implementing best practices, the maritime industry can enhance vessel safety and resilience against flooding risks.
Happy Boating!
Share Emergency Bilge Suction Valve in Ships’ Engine Rooms with your friends and leave a comment below with your thoughts.
Read Shipboard Oil Pollution Emergency Plan (SOPEP) until we meet in the next article.