Corrosion is a persistent challenge in industries reliant on metal structures, from marine vessels to underground pipelines. Sacrificial anodes, designed to corrode in place of critical components, are a cornerstone of corrosion prevention. Among the most widely used are zinc, aluminum, and magnesium anodes, each offering distinct properties tailored to specific environments and applications. This comprehensive guide compares these anodes based on their electrochemical properties, performance, applications, cost-effectiveness, and environmental impact, providing insights to help select the optimal anode for corrosion protection.
Understanding Sacrificial Anodes
Sacrificial anodes are integral to cathodic protection systems, which safeguard metal structures by allowing a more reactive metal to corrode preferentially. When connected to a structure, the anode releases electrons, neutralizing corrosive reactions on the protected metal. This process extends the lifespan of assets like ship hulls, pipelines, and water tanks.
Anodes function as the “sacrificial lamb” in a galvanic cell, where two dissimilar metals are immersed in an electrolyte, such as seawater or soil moisture. The less noble metal (the anode) corrodes, sparing the more noble metal (the structure). The effectiveness of an anode depends on its electrochemical potential, current capacity, and compatibility with the environment.
The Role of Anodes in Corrosion Protection
Corrosion occurs when metals react with environmental elements like oxygen, water, or salts, leading to structural degradation. Sacrificial anodes mitigate this by creating a controlled galvanic cell, where the anode corrodes instead of the structure. For example, on a steel ship in seawater, anodes attract corrosive agents, preserving the hull’s integrity.
Regular maintenance is critical, as anodes deplete over time. Inspections ensure timely replacement, maintaining continuous protection. The choice of anode material—zinc, aluminum, or magnesium—depends on factors like the structure’s material, the environment, and cost considerations.
Types of Sacrificial Anodes
While various anode materials exist, zinc, aluminum, and magnesium dominate due to their reactivity and availability. Each has unique electrochemical properties, making them suitable for specific applications.
Zinc Anodes
Zinc anodes are a staple in marine environments, prized for their reliability and cost-effectiveness in saltwater.
Properties of Zinc Anodes
Zinc anodes generate a voltage of approximately -1.05 volts relative to a silver/silver chloride reference electrode, providing a driving potential of about -0.75 volts when protecting bronze components. This electrochemical potential ensures effective cathodic protection in saline conditions. Zinc’s high current capacity allows it to protect large structures, and its predictable consumption rate simplifies maintenance.
Zinc anodes are lightweight, easy to install, and have a low self-consumption rate, extending their service life. Their ability to “slough” off oxide layers ensures consistent performance in dynamic marine environments.
Applications and Limitations
Zinc anodes excel in protecting offshore platforms, ship hulls, pipelines, and storage tanks in saltwater. Their corrosion by-products form a protective layer, shielding steel structures from corrosive agents.
However, zinc anodes are less effective in freshwater, where they form an insulating zinc hydroxide film, reducing their activity. In brackish water, this passivation can also occur, limiting their utility. Additionally, zinc anodes are less suitable for highly resistive soils due to low current output. Environmental concerns arise from cadmium activators in some zinc alloys, which are toxic to marine life.
Price of Zinc Anodes
Zinc anodes typically cost around $42 for standard marine applications (e.g., West Marine).
Aluminum Anodes
Aluminum anodes are versatile, performing well in both marine and soil environments, and are increasingly favored for their longevity and environmental benefits.
Properties of Aluminum Anodes
Aluminum anodes, typically alloys with zinc and indium, generate a voltage of -1.1 volts, offering a slightly higher driving potential than zinc (-0.8 volts for bronze protection). Their electrochemical capacity is over three times that of zinc for the same mass, enabling longer-lasting protection. Aluminum maintains a stable potential, reducing the risk of localized corrosion.
Lightweight and easy to handle, aluminum anodes are ideal for large-scale installations. Alloys prevent the formation of insulating oxide films, ensuring consistent performance.
Applications and Limitations
Aluminum anodes are used in offshore platforms, underground pipelines, water storage tanks, and harbor structures. They perform well in saline and brackish water, making them suitable for vessels transitioning between water types.
In freshwater with high chloride concentrations, aluminum anodes may experience increased consumption rates, requiring careful monitoring. The quality of the alloy is critical, as substandard alloys may underperform. Aluminum anodes are subject to restrictions in ballast and cargo tanks due to potential explosive atmospheres.
Price of Aluminum Anodes
Aluminum anodes are generally priced at around $32 for marine applications (e.g., West Marine), offering cost savings over zinc due to lower weight and longer lifespan.
Magnesium Anodes
Magnesium anodes are the go-to choice for freshwater and high-resistivity soil environments, offering unmatched driving potential.
Properties of Magnesium Anodes
Magnesium anodes produce a voltage of -1.6 volts, providing a driving potential of -1.3 volts for bronze protection—the highest among the three. This high potential ensures efficient corrosion protection in low-conductivity environments. Magnesium’s self-cleaning properties disperse corrosion by-products, reducing coating damage and maintaining effectiveness.
Applications and Limitations
Magnesium anodes are ideal for protecting buried pipelines, storage tanks, and water heaters in freshwater and resistive soils. Their high current output makes them effective in challenging conditions.
However, magnesium anodes have a high consumption rate, requiring frequent replacements. In saltwater, they corrode rapidly and may generate hydrogen gas, posing safety risks. They are unsuitable for wooden-hulled boats due to potential electrochemical decay and are less effective in saline environments.
Price of Magnesium Anodes
Magnesium anodes cost approximately $55 for standard applications (e.g., West Marine), reflecting their higher reactivity and shorter lifespan.
Comparative Analysis
Choosing the right anode requires evaluating performance, cost-effectiveness, and environmental impact. Below is a detailed comparison.
Performance Comparison
Property | Zinc | Aluminum | Magnesium |
---|---|---|---|
Voltage (V) | -1.05 | -1.1 | -1.6 |
Driving Potential (V) | -0.75 (bronze) | -0.8 (bronze) | -1.3 (bronze) |
Current Capacity | 100 (datum, e.g., 150 days) | 130–150 (195–225 days) | 30 (50 days) |
Best Environment | Saltwater | Saltwater, brackish, some freshwater | Freshwater, resistive soils |
Self-Cleaning | Moderate (sloughing) | Low (cratered erosion) | High (disperses by-products) |
- Zinc: Reliable in saltwater, with even corrosion and predictable maintenance. Less effective in freshwater or resistive soils.
- Aluminum: Versatile, with high capacity and stable potential. Suitable for multiple water types but requires quality alloys.
- Magnesium: Excels in freshwater and resistive soils due to high driving potential but consumes quickly and is unsuitable for saltwater.
Cost-Effectiveness Analysis
Anode | Initial Cost | Lifespan | Maintenance | Overall Cost-Effectiveness |
---|---|---|---|---|
Zinc | $42 | 150 days | Predictable | High in saltwater |
Aluminum | $32 | 195–225 days | Moderate | Highest across environments |
Magnesium | $55 | 50 days | Frequent | Moderate in freshwater |
- Zinc: Competitive initial cost and predictable lifespan make it cost-effective in saltwater. Maintenance is straightforward.
- Aluminum: Lower initial cost and longer lifespan offer superior cost-effectiveness, especially for vessels in varied waters.
- Magnesium: Higher cost and frequent replacements reduce cost-effectiveness, but performance in freshwater justifies use.
Environmental Impact Assessment
Anode | Environmental Impact | Recyclability | Considerations |
---|---|---|---|
Zinc | Moderate (cadmium toxicity) | High | Toxic activators harm marine life |
Aluminum | Low (less toxic activators) | High | Environmentally friendlier |
Magnesium | Moderate (hydrogen gas, high consumption) | Moderate | Requires careful management |
- Zinc: Cadmium activators pose environmental risks, though recycling mitigates impact.
- Aluminum: Lower toxicity and recyclability make it the most environmentally friendly option.
- Magnesium: High consumption and potential hydrogen gas generation require environmental management.
Chart: Anode Selection Workflow
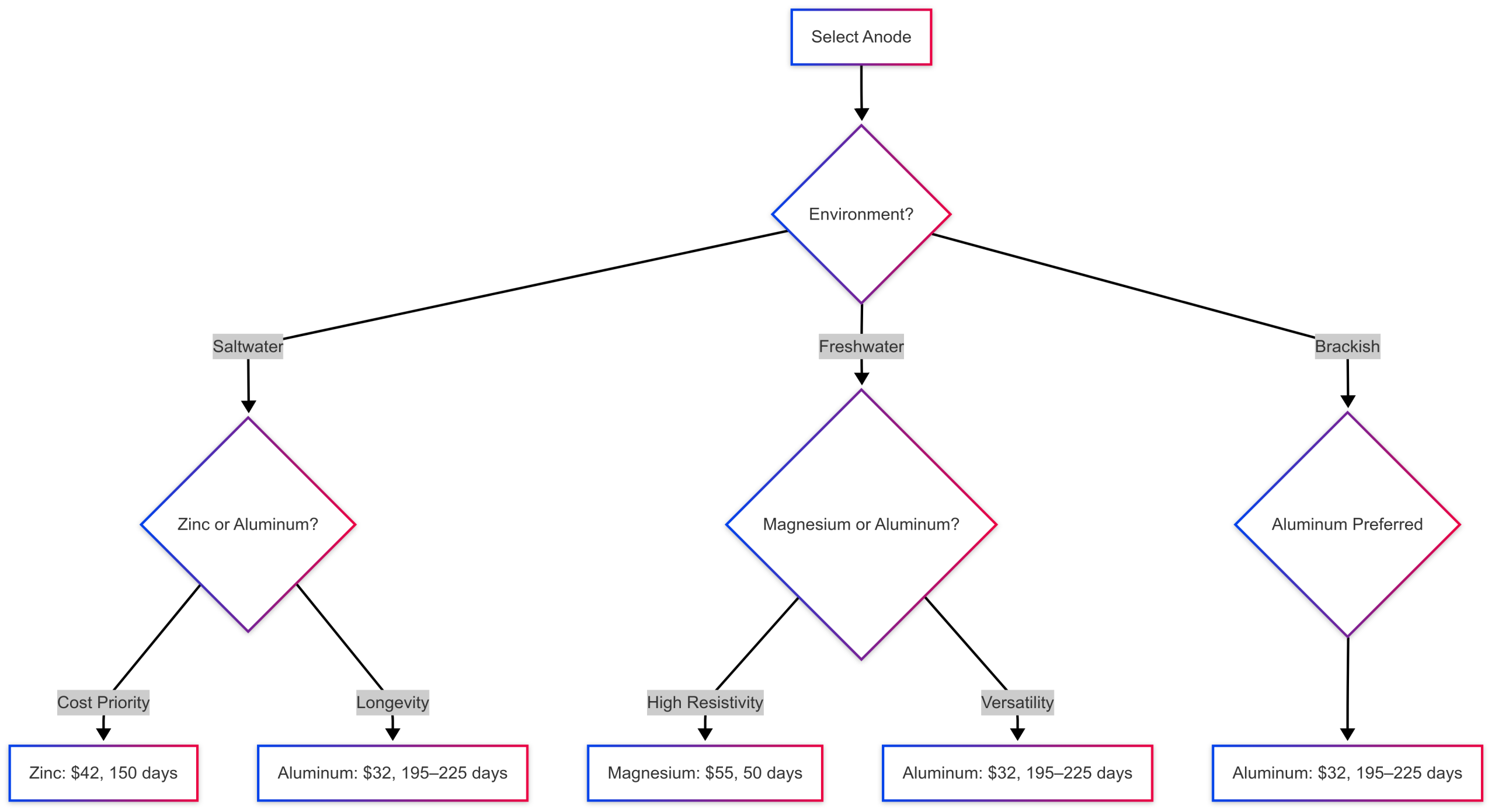
This workflow guides anode selection based on environment, cost, and longevity, highlighting aluminum’s versatility.
Practical Considerations for Anode Selection
Selecting the right anode involves balancing performance, cost, and environmental factors. Key considerations include:
- Water Type: Use zinc or aluminum in saltwater, aluminum in brackish water, and magnesium or aluminum in freshwater. Avoid zinc in freshwater and magnesium in saltwater.
- Structure Material: Ensure compatibility to avoid overprotection. For example, magnesium can overprotect aluminum hulls, causing damage.
- Boat Usage: Vessels transitioning between water types benefit from aluminum’s versatility. Stationary vessels in saltwater may prefer zinc for cost and sloughing properties.
- Maintenance: Aluminum requires less frequent replacement, while magnesium demands regular inspections due to rapid consumption.
- Environmental Regulations: Opt for aluminum in environmentally sensitive areas to minimize toxicity.
Installation and Maintenance Tips
- Ensure Electrical Contact: Clean surfaces to ensure bare metal contact. Use a multimeter to verify conductivity.
- Avoid Painting: Paint inhibits anode function. Keep anodes uncoated.
- Regular Inspections: Check anodes every few months in saltwater or annually in freshwater. Replace when 50% eroded.
- Avoid Mixing Anodes: Mixing metals (e.g., zinc on hull, aluminum on drive) can reduce effectiveness.
- Internal Anodes: Don’t neglect pencil anodes in cooling systems, which protect internal components.
Identifying Anode Material
Distinguishing between zinc, aluminum, and magnesium anodes can be challenging, especially for used or unmarked anodes. Use these clues:
- Weight: Magnesium is lightest (e.g., 1.6 lbs for a standard anode), followed by aluminum (3 lbs), and zinc (7.5 lbs).
- Appearance: Magnesium is dark gray with a dull, rough surface. Zinc is darker and shinier, while aluminum may have a slight gold tint.
- Corrosion Patterns: Magnesium turns yellow and porous, aluminum forms white, craggy peaks, and zinc produces fine, gray oxide dust.
For precise identification, use a reference cell to measure voltage or consult a corrosion specialist.
Industry Standards and Quality
Anode performance depends on alloy quality. Substandard anodes may fail prematurely, leading to costly corrosion damage. Adhere to these specifications:
- Zinc: MIL-DTL-18001L
- Aluminum: MIL-DTL-24779(SH)
- Magnesium: MIL-A-21412
Reputable manufacturers, such as Deyuan Marine, comply with standards like GB 4948 and offer certifications (e.g., CCS, BV, ABS). High-quality aluminum anodes, like Navalloy (aluminum/zinc/indium alloy), resist passivation and ensure consistent performance.
Conclusion
Zinc, aluminum, and magnesium anodes each play a vital role in corrosion protection, with distinct strengths and limitations. Zinc is reliable and cost-effective in saltwater, aluminum offers versatility and environmental benefits across water types, and magnesium excels in freshwater and resistive soils despite higher costs. By evaluating performance, cost-effectiveness, and environmental impact, stakeholders can select the optimal anode for their needs.
For marine vessels, aluminum is often the best choice due to its longevity, lower cost, and environmental friendliness. In freshwater or resistive soils, magnesium’s high driving potential is unmatched, though it requires diligent maintenance. Zinc remains a solid option for stationary saltwater applications. Consulting corrosion experts and adhering to industry standards ensures effective protection, safeguarding assets and minimizing environmental impact.
Happy Boating!
Share Comparing Zinc, Aluminum, and Magnesium Anodes with your friends and leave a comment below with your thoughts.
Read Boating at Night: Tips for Safe Navigation After Dark until we meet in the next article.