Learn essential do’s and don’ts for efficient marine boiler operations, ensuring safety, compliance, and optimal performance on ships.
Marine boilers are the backbone of a ship’s steam systems, powering propulsion, electrical generation, heating, and auxiliary machinery. Operating these complex, high-pressure systems efficiently while maintaining safety is a critical responsibility for marine engineers. Improper operation or maintenance can lead to inefficiencies, equipment damage, or catastrophic accidents, including explosions or fires that endanger lives and property. This comprehensive guide outlines the essential do’s and don’ts for marine boiler operations, integrating safety protocols, design considerations, maintenance practices, and operational strategies to ensure reliability, efficiency, and compliance with international maritime standards.
The Importance of Marine Boilers
Marine boilers generate steam for multiple critical functions on ships:
- Propulsion: In steam-powered vessels, boilers produce high-pressure steam to drive turbines or engines, providing the thrust needed for navigation.
- Electrical Power: Steam powers turbines connected to generators, supplying electricity for lighting, navigation systems, and other equipment.
- Heating: Steam heats crew accommodations, fuel tanks, and cargo, maintaining optimal temperatures for comfort and operational efficiency.
- Cargo Handling: On tankers, steam ensures proper viscosity of heavy fuels or chemicals for pumping and transfer.
- Auxiliary Systems: Steam drives pumps, compressors, and winches, supporting various shipboard operations.
Given their critical role, boilers must operate within strict safety and efficiency parameters to prevent accidents and maintain vessel performance. Historical data highlights the risks: boiler-related accidents have caused significant property damage and loss of life due to improper operation or neglected maintenance. This guide provides actionable do’s and don’ts to mitigate these risks and optimize boiler performance.
Boiler Types and Their Design
Marine boilers primarily fall into two categories: water tube boilers and fire tube (smoke tube) boilers. Each has distinct design features, operational characteristics, and applications, influencing how they are operated and maintained.
Water Tube Boilers: High-Performance Systems
Water tube boilers, such as the Foster Wheeler ESD-type, are designed for high-pressure applications, making them ideal for main propulsion and high-demand systems.
- Design Features:
- Steam and Water Drums: The steam drum stores and separates steam, while the water drum distributes feedwater to generating tubes.
- Generating Tubes: Vertical tubes connect the drums, where water is heated to produce steam.
- Superheater: Heats steam above saturation temperature for dry, high-energy steam suitable for turbines.
- Economizer: Preheats feedwater using waste exhaust gases, improving efficiency by 5-15%.
- Burner and Baffles: Optimize combustion and heat transfer.
- Operational Characteristics:
- Pressure Range: 60-150 bar.
- Steam Production: 10,000-500,000 kg/h.
- Efficiency: 85-90%.
- Start-up Time: 30-60 minutes.
- Applications: Main propulsion, naval systems, superheated steam needs.
- Advantages:
- High-pressure capability.
- Superior thermal efficiency.
- Modular design for easier maintenance.
- Lower explosion risk due to distributed pressure containment.
- Disadvantages:
- Complex operation requiring skilled personnel.
- Sensitive to water quality.
- Higher initial cost.
Fire Tube (Smoke Tube) Boilers: Compact and Reliable
Fire tube boilers, such as Cochran boilers, are suited for auxiliary systems requiring low to moderate steam volumes.
- Design Features:
- Hemispherical Furnace: Enhances heat distribution and structural strength.
- Fire Tubes: Hot gases pass through tubes submerged in water, transferring heat via conduction.
- Composite Functionality: Can use oil firing or waste exhaust heat, improving efficiency.
- Access Points: Manholes and handholes facilitate maintenance.
- Operational Characteristics:
- Pressure Range: Up to 25 bar.
- Steam Production: 500-20,000 kg/h.
- Efficiency: 75-80%.
- Start-up Time: 15-30 minutes.
- Applications: Heating, fuel conditioning, small power generation.
- Advantages:
- Compact and simple design.
- Quick response to steam demand.
- Tolerant of imperfect water quality.
- Easy maintenance by general crew.
- Disadvantages:
- Limited pressure and efficiency.
- Higher explosion risk if mishandled.
- Requires full shutdown for tube repairs.
Comparative Analysis
The following table summarizes the key differences between water tube and fire tube boilers:
Feature | Water Tube Boiler | Fire Tube Boiler |
---|---|---|
Pressure Range | 60-150 bar | 10-25 bar |
Steam Production | 10,000-500,000 kg/h | 500-20,000 kg/h |
Efficiency | 85-90% | 75-80% |
Start-up Time | 30-60 minutes | 15-30 minutes |
Applications | Main propulsion, high-pressure systems | Auxiliary systems, heating |
Safety Risk | Lower (distributed pressure) | Higher (single pressure vessel) |
Maintenance Complexity | High (specialized skills needed) | Low (general crew can handle) |
Footprint | Taller, narrower | Longer, lower profile |
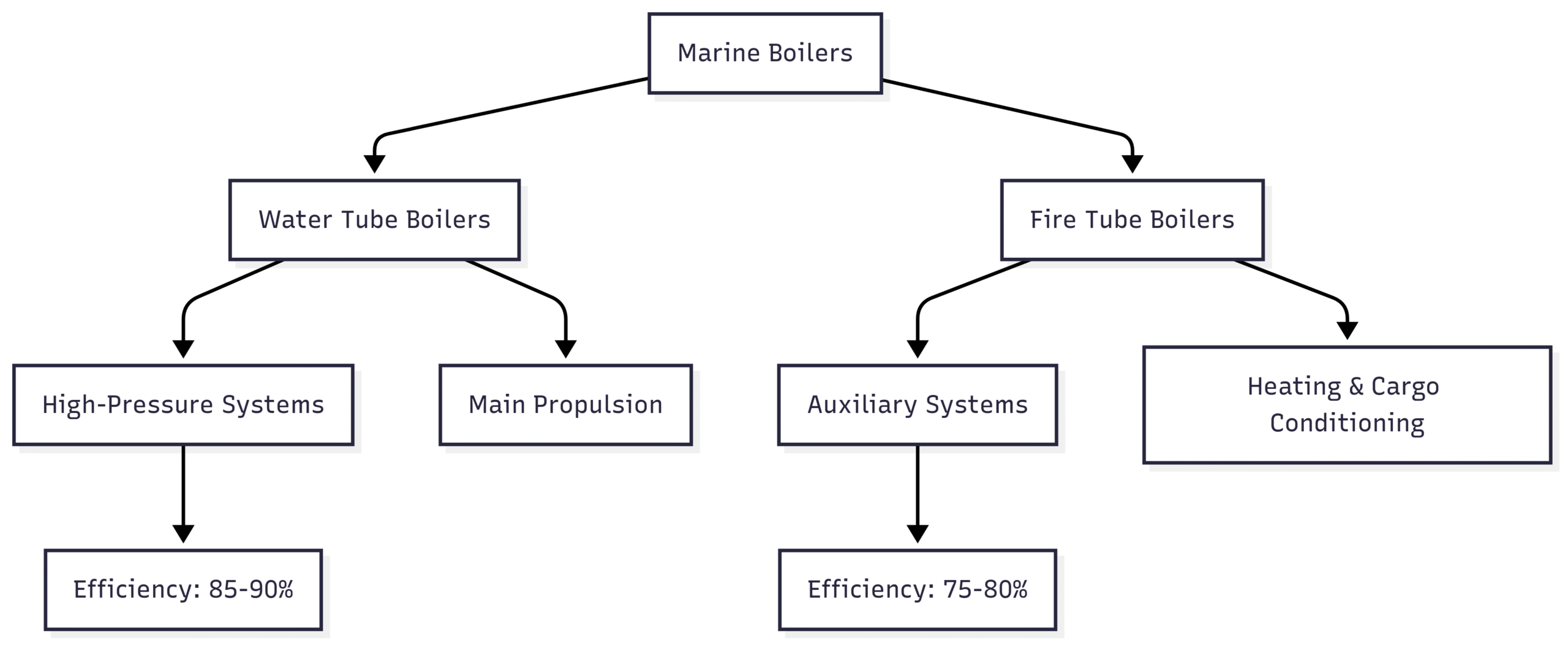
Safety in Boiler Construction
The construction of marine boilers must adhere to stringent standards to ensure safety and reliability. Key considerations include:
- Regulatory Compliance: Boilers must meet international standards like SOLAS Chapter II-1 and classification society rules (e.g., Lloyd’s Register, DNV GL). These regulations specify design parameters, pressure ratings, and safety margins.
- Material Selection: Components are made from high-quality alloys (e.g., carbon steel with chromium or molybdenum) to withstand high temperatures, pressures, and corrosion from saline environments.
- Redundancy: Critical systems, such as safety valves and water level controls, are duplicated to ensure fail-safe operation.
- Safety Devices: Boilers are equipped with pressure relief valves, flame detectors, high-temperature alarms, and automated shutdown systems, all requiring regular calibration.
Proper planning of boiler placement in the engine room ensures accessibility for maintenance, while piping systems are designed to accommodate thermal expansion, reducing stress on components.
Safety in Boiler Maintenance
Regular maintenance is crucial to prevent failures and maintain efficiency. Key practices include:
- Routine Inspections: Use non-destructive testing (NDT) methods like ultrasonic or dye penetrant inspections to detect cracks, wear, or corrosion in tubes, valves, and other components.
- Cleaning: Remove scale and deposits from boiler tubes using approved chemicals or mechanical methods to prevent overheating and maintain heat transfer efficiency.
- Refractory Maintenance: Inspect and repair furnace linings to prevent cracking or spalling, which can compromise safety.
- Safety Device Testing: Regularly test pressure relief valves, flame detectors, and water level alarms to ensure functionality during emergencies.
- Water Treatment: Implement proper water treatment to prevent corrosion and scaling, which can weaken components and reduce efficiency.
- Documentation: Maintain detailed logs of maintenance activities to comply with the ISM Code and track performance trends.
Predictive maintenance strategies, such as condition-based monitoring (CBM), use real-time data to anticipate failures, reducing downtime and enhancing safety. Crew training on maintenance procedures, safe handling, and emergency protocols is essential, often supplemented by simulator-based training.
Safety in Boiler Operation
Safe operation of marine boilers requires strict adherence to protocols and continuous monitoring. Key operational considerations include:
- Operating Procedures: Follow established procedures for startup, shutdown, and normal operation. Pre- and post-purge the furnace during firing to prevent fuel buildup, and keep air vents open during initial firing and shutdown.
- Combustion Control: Maintain proper air-fuel mixtures to ensure safe combustion and minimize explosion risks. Monitor exhaust emissions to comply with MARPOL Annex VI and optimize efficiency.
- Steam Quality: Use water treatment systems and deaerators to prevent scaling or corrosion, ensuring high-quality steam.
- Emergency Preparedness: Train crews in emergency shutdowns, firefighting, and steam leak containment. Conduct regular drills to improve response effectiveness.
- Scalding Prevention: Use insulation, protective barriers, and personal protective equipment (PPE) to minimize exposure to high-temperature surfaces and steam leaks.
Digital monitoring systems, such as SCADA or IoT-based solutions, provide real-time oversight of steam pressure, temperature, and water levels, enabling early detection of issues.
Essential Do’s for Efficient Boiler Operations
To ensure safe and efficient boiler operations, marine engineers should follow these best practices:
- Follow Operating Procedures: Adhere to correct procedures for lighting up the boiler from a cold condition. Pre- and post-purge the furnace and keep the air vent open during startup and shutdown to prevent fuel accumulation.
- Regular Blowdown: Perform gauge glass blowdown once per watch and boiler blowdown daily to control chloride levels and remove impurities like oil or foam. Conduct scum blowdown if floating contaminants are detected.
- Soot Blowing: Regularly perform soot blowing to maintain the heat transfer efficiency of boiler tubes and prevent fires caused by soot accumulation.
- Monitor Smoke: Check funnel smoke during each watch to assess combustion quality. Excessive smoke indicates incomplete combustion, requiring immediate attention.
- Lubrication: Lubricate mechanical parts and linkages regularly to ensure smooth operation and prevent wear.
- Test Emergency Shutdown: Verify the functionality of emergency shutdown systems, located in the engine control room (ECR), as per the company’s Safety Management System (SMS).
- Inspect Valves and Dampers: Ensure fuel line valves, steam valves, safety valves, and quick-closing valves operate correctly.
- Address Leakages: Promptly repair steam leaks to maintain efficiency and prevent energy loss.
- Monitor Furnace: Regularly inspect the furnace for refractory deterioration or fuel dripping near the burner, addressing defects immediately.
- Firefighting Readiness: Ensure boiler-specific firefighting equipment (e.g., foam extinguishers, high-pressure jet fog systems) is functional. Conduct regular drills to train crew in boiler fire response.
Critical Don’ts for Boiler Operations
Avoiding common mistakes is equally important to prevent accidents and maintain efficiency:
- Untrained Operators: Never allow assistant engineers or untrained personnel to operate the boiler, especially during startup from a cold condition.
- Excessive Blowdown: Avoid over-blowdown, as it introduces cold feedwater, reducing thermal efficiency and causing thermal stress.
- Soot Blowing at High Load: Do not operate soot blowers when the boiler is at high load, as this can disrupt combustion and damage tubes.
- Ignoring Abnormalities: Address unusual sounds, smoke, flame quality, or other parameters immediately to prevent escalation.
- Overloading: Avoid regular operation at high loads, as it causes excessive stress and potential tube failure. Overload only when necessary due to steam demand.
- Sea Water Contamination: Never use seawater in the boiler. If seawater enters the hot well (e.g., due to condenser leaks), shut down the boiler and rectify the issue.
- Operating with Leaks: Do not operate the boiler with leaking water tubes. Repair leaks promptly to prevent damage.
- Relying Solely on Remote Indicators: Verify water levels using local gauge glasses, as remote indicators in the control room may be inaccurate.
- Leaving Furnace Door Open: Close the furnace door after burner cleaning or inspections to prevent heat loss and safety hazards.
- Skipping Maintenance: Perform periodic maintenance of the boiler and its auxiliaries to maintain efficiency and prevent long-term degradation.
Boiler Water Testing and Quality Control
Proper water quality is critical to boiler longevity and efficiency. Poor water quality leads to scale buildup, corrosion, and foaming, which can reduce efficiency by up to 15%, damage components, and create safety hazards. Key water tests include:
- pH (9.5-11.5): Prevents corrosion and optimizes chemical treatment.
- Phosphate (20-50 ppm): Prevents scale by forming removable sludge.
- Hydrazine (0.1-0.2 ppm): Removes oxygen to prevent pitting corrosion.
- Chloride (<300 ppm): Detects seawater contamination, which accelerates corrosion.
- Total Dissolved Solids (TDS, 2,000-3,500 ppm): Determines blowdown frequency to prevent foaming.
Testing Procedures:
- Collect samples using cooling coils and clean containers.
- Perform critical tests (pH, phosphate) daily and comprehensive tests weekly.
- Adjust chemical dosing and increase blowdown as needed based on results.
Neglecting water testing can lead to higher fuel costs, unexpected downtime, and safety risks. Proper treatment extends boiler life and ensures reliable operation.
Safety Valves: The Last Line of Defense
Safety valves are critical for preventing over-pressurization. Maritime regulations mandate:
- Quantity: At least two independent valves per boiler.
- Pressure Settings: Activate at 3% above working pressure, with pressure not exceeding 10% above set pressure under maximum firing conditions.
- Performance: Open fully, handle maximum steam capacity, and reseat properly.
Modern valves feature precision-machined lips and waste steam pistons for optimal flow and stability. Regular testing, including accumulation tests, ensures reliability.
Economizer and Superheater: Enhancing Efficiency
- Economizer: Recovers waste heat from exhaust gases (250-400°C), preheating feedwater by 50-100°C. This reduces fuel consumption by 5-15% and lowers thermal stress.
- Superheater: Heats steam 50-150°C above saturation, producing dry steam that improves turbine efficiency by 15-20%.
These components, made from corrosion-resistant alloys, are strategically placed in the exhaust path to maximize heat recovery and steam quality.
Boiler Survey Process
Mandatory boiler surveys, conducted every 30 months (or annually for older boilers), ensure safety and compliance:
- Mountings Inspection: Verify safety valves, control systems, and gauges.
- Structural Examination: Check for corrosion, distortion, or tube thinning.
- Internal Assessment: Inspect tube ends, drums, and heating surfaces for damage.
Post-survey repairs and documentation ensure the boiler meets operational standards.
Case Studies: Lessons from Incidents
- Over-Pressurization Incident: A faulty safety valve caused a boiler to exceed safe pressure limits, leading to a near-explosion. Regular testing could have prevented this.
- Tube Failure Due to Scale: Scale buildup caused localized overheating, resulting in tube rupture. Routine water testing and blowdown mitigated future risks.
- Successful Predictive Maintenance: A vessel using CBM detected early tube wear via ultrasonic testing, preventing a costly failure.
These examples underscore the importance of adherence to safety protocols and proactive maintenance.
Conclusion
Efficient and safe marine boiler operations require a holistic approach encompassing robust construction, diligent maintenance, and strict operational protocols. By adhering to international standards, using high-quality materials, and implementing redundant safety systems, boilers can be constructed to withstand harsh marine environments. Regular maintenance, including inspections, cleaning, and water treatment, ensures reliability and efficiency. Operational best practices, guided by the do’s and don’ts outlined, minimize risks and optimize performance. Continuous crew training, real-time monitoring, and emergency preparedness further enhance safety. By fostering a culture of vigilance and compliance, ship operators can protect crew members, comply with regulations, and ensure the longevity and efficiency of marine boilers, safeguarding the heart of the ship’s steam systems.
Happy Boating!
Share Do’s and Don’ts for Efficient Boiler Operations On Ships with your friends and leave a comment below with your thoughts.
Read Weathertight or watertight doors, that’ s the question until we meet in the next article.