Discover how AI revolutionizes predictive maintenance in maritime shipping, enhancing efficiency, safety, and sustainability while reducing costs.
The maritime industry, a backbone of global trade, faces persistent challenges: high operational costs, safety risks, environmental regulations, and the ever-present threat of equipment failure. Artificial Intelligence (AI) is emerging as a game-changer, particularly in predictive maintenance, where it transforms how ships are maintained, operated, and optimized. By leveraging real-time data, advanced algorithms, and predictive modeling, AI minimizes downtime, enhances safety, reduces costs, and supports sustainability. This article explores the profound impact of AI-driven predictive maintenance on the maritime sector, delving into its mechanisms, benefits, implementation, and future potential.
The Need for Predictive Maintenance in Maritime Operations
Ships operate in harsh environments, enduring extreme weather, corrosive saltwater, and constant mechanical stress. Traditionally, maintenance has been reactive—fixing issues after they occur—or preventive, based on fixed schedules. Both approaches are inefficient. Reactive maintenance leads to costly downtime and safety risks, while preventive maintenance often results in unnecessary repairs, wasting resources. Predictive maintenance, powered by AI, offers a proactive solution, using data to anticipate failures before they happen.
Why Predictive Maintenance Matters
- Downtime Costs: A single day of downtime can cost shipping companies tens of thousands of dollars in lost revenue and penalties.
- Safety Risks: Equipment failures at sea can endanger crews and cargo, leading to accidents or environmental disasters.
- Environmental Impact: Poorly maintained systems consume more fuel, increasing emissions and violating regulations like the International Maritime Organization’s (IMO) sulphur cap.
- Operational Efficiency: Optimized maintenance ensures vessels operate at peak performance, reducing fuel consumption and extending component lifespans.
AI-driven predictive maintenance addresses these challenges by shifting from guesswork to data-driven precision, revolutionizing maritime operations.
How AI Powers Predictive Maintenance
At the heart of AI-driven predictive maintenance is the ability to process vast amounts of data in real-time, identifying patterns and anomalies that signal potential issues. Here’s how it works:
1. Real-Time Data Collection
Modern ships are equipped with thousands of sensors monitoring critical systems, including:
- Engines: RPMs, fuel consumption, temperature, pressure, vibrations.
- Hull: Stress patterns, corrosion, structural integrity.
- Auxiliary Systems: Pumps, generators, HVAC, navigation equipment.
These sensors generate terabytes of data daily, which AI systems aggregate and analyze continuously.
2. Advanced Algorithms and Machine Learning
AI employs machine learning (ML) models trained on historical data, such as maintenance logs, failure records, and operational metrics. These models:
- Detect anomalies (e.g., a slight increase in engine vibration).
- Predict when components are likely to fail based on usage patterns and environmental factors.
- Recommend specific maintenance actions, such as inspecting a fuel injector or realigning a drive shaft.
For example, an AI system might detect a 2% increase in fuel consumption, cross-reference it with historical data, and identify a clogged fuel injector as the likely cause, prompting preemptive action.
3. Predictive Modeling
AI builds predictive models that forecast component lifespans and failure probabilities. These models consider:
- Historical failure rates.
- Real-time sensor data.
- External factors like weather, sea conditions, and operational load.
This allows operators to plan maintenance at optimal times, avoiding disruptions.
4. Integration with Digital Twins
Digital twins—virtual replicas of physical vessels—enhance predictive maintenance by simulating real-time performance. Fed with sensor data, digital twins allow operators to:
- Monitor vessel conditions remotely.
- Simulate failure scenarios to assess risks.
- Optimize maintenance schedules without risking actual assets.
Digital twins also support crew training, enabling simulations of emergency responses in a risk-free environment.
Chart: AI Predictive Maintenance Workflow
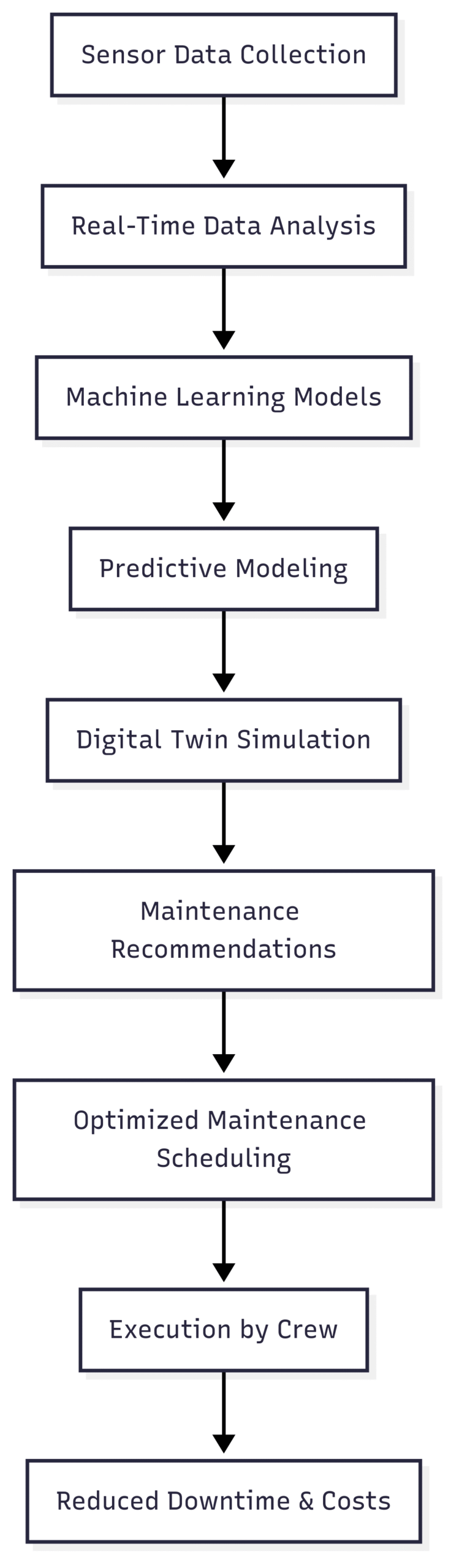
Key Benefits of AI-Driven Predictive Maintenance
AI transforms predictive maintenance into a strategic asset, delivering measurable benefits across efficiency, safety, cost, and sustainability.
1. Reduced Downtime and Costs
By anticipating failures, AI minimizes unplanned repairs, which can cost $50,000–$100,000 per day for a large cargo vessel. Proactive maintenance also reduces:
- Labor costs by eliminating unnecessary inspections.
- Spare parts expenses by targeting only at-risk components.
- Fuel costs through optimized system performance.
Table: Cost Savings from AI Predictive Maintenance
Aspect | Traditional Maintenance | AI Predictive Maintenance | Savings Potential |
---|---|---|---|
Downtime Costs | $50,000/day | $10,000/day | 80% reduction |
Spare Parts Usage | 20% overstock | 5% overstock | 75% reduction |
Fuel Efficiency | Baseline | 5–10% improvement | $100,000/year |
Labor Hours | 500 hours/year | 300 hours/year | 40% reduction |
2. Enhanced Safety
AI prevents equipment failures that could lead to accidents, such as engine fires or hull breaches. By analyzing sensor data, AI:
- Detects hazards like overheating bearings or structural weaknesses.
- Issues real-time alerts to crews.
- Reduces the risk of environmental incidents, such as oil spills.
For instance, AI might detect abnormal vibrations in a propeller shaft, prompting inspection before it causes a catastrophic failure.
3. Extended Component Lifespan
Proactive maintenance extends the life of critical components, such as engines and pumps, by 20–30%. This reduces capital expenditures and logistical challenges associated with replacements.
4. Environmental Sustainability
AI-optimized systems operate more efficiently, reducing fuel consumption and emissions by 5–15%. This helps comply with IMO regulations and supports sustainability goals. Additionally, preventing failures minimizes the risk of environmental hazards like fuel leaks.
5. Optimized Maintenance Schedules
AI considers operational factors—vessel location, port availability, and crew schedules—to plan maintenance at the least disruptive times. This ensures vessels remain operational, maximizing revenue.
Case Study: AI in Action
Consider the cargo ship Voyager, operating between Rotterdam and Singapore. Its AI system detects a 3% increase in fuel consumption in the main engine. By analyzing sensor data and maintenance logs, the AI identifies a misaligned fuel injector. The system:
- Recommends replacing the injector at the next port.
- Alerts the crew with a diagnostic report.
- Schedules maintenance during a planned stop, avoiding downtime.
The repair costs $5,000, compared to $50,000 for an emergency engine overhaul. The ship avoids a 2-day delay, saving $100,000 in downtime costs and maintaining its delivery schedule.
Implementing AI Predictive Maintenance
Adopting AI-driven predictive maintenance requires strategic planning, investment, and workforce training. Here’s how maritime companies can integrate this technology:
1. Upgrading Infrastructure
Modern ships are AI-ready, but older vessels need retrofitting with:
- Advanced sensors for real-time data collection.
- High-bandwidth networks to handle data transmission.
- Cybersecurity measures to protect AI systems.
Cost Estimate for Retrofitting
Component | Cost (USD) |
---|---|
Sensors (500 units) | $100,000 |
Network Upgrade | $50,000 |
Cybersecurity | $20,000 |
Total | $170,000 |
2. Partnering with AI Providers
Collaborate with tech firms like MetaOPT or IBM to deploy tailored AI solutions. These partnerships provide:
- Cutting-edge algorithms.
- Integration support.
- Ongoing system updates.
3. Training the Workforce
Crew members must learn to interpret AI alerts and integrate them into workflows. Training programs should include:
- Virtual simulations of AI-driven maintenance scenarios.
- Hands-on workshops with real-world applications.
- Continuous learning to keep pace with AI advancements.
4. Starting with a Pilot Project
Begin with a single vessel or component (e.g., main engine) to test AI systems. Scale up after validating results, ensuring minimal disruption.
Chart: Implementation Process
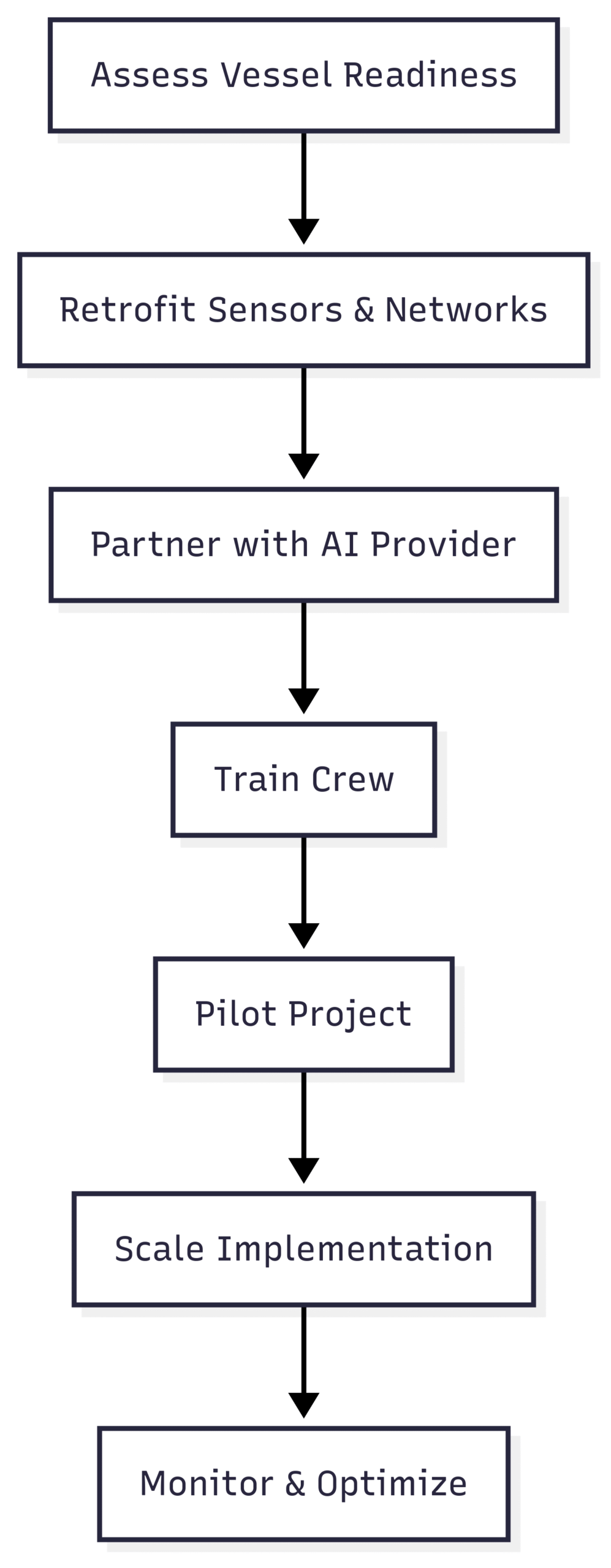
Challenges and Risks
While AI offers transformative benefits, it comes with challenges:
- Data Quality: Inaccurate or incomplete data can lead to false predictions. Regular sensor calibration is essential.
- Initial Costs: Retrofitting and training require upfront investment, though ROI is achieved within 1–2 years.
- Cybersecurity: AI systems are vulnerable to hacking, necessitating robust protections.
- Workforce Resistance: Crews may resist adopting new technology, requiring change management strategies.
Mitigating these risks involves rigorous testing, ongoing monitoring, and fostering a culture of innovation.
The Future of AI in Maritime Predictive Maintenance
As AI technology evolves, its role in predictive maintenance will expand:
- Autonomous Maintenance: AI could automate minor repairs using robotic systems, reducing human intervention.
- Integration with Autonomous Ships: Predictive maintenance will be critical for crewless vessels, ensuring reliability.
- Advanced Analytics: Future AI models will incorporate external data, such as global weather patterns or supply chain disruptions, for even more accurate predictions.
- Sustainability Focus: AI will further optimize emissions, supporting net-zero goals.
Economic and Strategic Implications
Investing in AI predictive maintenance positions maritime companies as industry leaders. Key advantages include:
- Competitive Edge: Reduced costs and faster delivery attract more clients.
- Regulatory Compliance: AI ensures adherence to IMO and environmental standards, avoiding fines.
- Innovation Leadership: Early adopters set industry benchmarks, attracting partnerships and talent.
Table: Strategic Benefits
Benefit | Impact |
---|---|
Market Competitiveness | 15% increase in customer retention |
Regulatory Compliance | 100% reduction in fines |
Innovation Leadership | 20% increase in partnerships |
Conclusion: Navigating the AI Era
AI-driven predictive maintenance is not just a technological upgrade—it’s a strategic revolution reshaping the maritime industry. By anticipating failures, optimizing schedules, and enhancing safety, AI empowers shipping companies to navigate challenges with precision and confidence. As global trade grows and environmental pressures mount, embracing AI is a commitment to efficiency, sustainability, and competitiveness.
Maritime leaders must act decisively:
- Invest in AI: Allocate resources to adopt cutting-edge systems.
- Partner with Experts: Leverage tech providers for seamless integration.
- Cultivate Innovation: Train crews and foster a forward-thinking culture.
- Monitor Progress: Continuously refine AI strategies to maximize ROI.
With solutions like MetaOPT, maritime companies can chart a course for a smarter, safer, and more sustainable future, ensuring their fleets thrive in the AI era.
FAQs
How does AI predict maintenance needs on ships?
AI analyzes sensor data with machine learning models, comparing real-time metrics to historical patterns to identify potential failures.
Can AI maintenance systems integrate with older ships?
Yes, older vessels can be retrofitted with sensors and networks, though upgrades require careful planning.
What are the costs of AI in predictive maintenance?
Initial costs range from $150,000 to $300,000 per vessel, with savings of $500,000–$2M annually from reduced downtime and repairs.
How does AI improve safety in maritime operations?
AI detects hazards, issues real-time alerts, and prevents accidents by identifying risks like overheating or structural weaknesses.
What is the environmental impact of AI predictive maintenance?
AI reduces fuel consumption and emissions by 5–15% and prevents spills, supporting IMO compliance and eco-friendly operations.
How do digital twins support AI maintenance?
Digital twins simulate vessel performance, enabling remote monitoring, failure prediction, and crew training.
About MetaOPT
MetaOPT provides AI-driven solutions for maritime operations, helping fleets optimize maintenance, reduce costs, and enhance sustainability. Visit MetaOPT.com to learn more.
Happy Boating!
Share Artificial Intelligence in Predictive Maintenance for Ships with your friends and leave a comment below with your thoughts.
Read STCW-Compliant VR Maritime Training until we meet in the next article.