Master MAN marine engine cooling system maintenance with expert tips from 805 Marine Mechanic. Ensure longevity, efficiency, and performance.
Marine diesel engines are the heart of many vessels, from recreational yachts to commercial ships, providing reliable power for propulsion and auxiliary systems. Proper maintenance, particularly of the cooling system, is critical to ensuring these engines deliver optimal performance, fuel efficiency, and longevity. Neglecting routine maintenance can lead to overheating, corrosion, and costly repairs, potentially leaving you stranded at sea. This comprehensive guide, enriched with expert insights from 805 Marine Mechanic and industry best practices, explores the intricacies of marine diesel engine maintenance, focusing on cooling system care. Whether you’re a seasoned boater in Ventura, the Channel Islands, or Santa Barbara, or a novice vessel operator, this article equips you with the knowledge to keep your engine running smoothly.
Understanding Marine Diesel Engines
Marine diesel engines differ from their automotive or industrial counterparts due to their unique operating environment. Constant exposure to water, salt, and humidity demands specialized components and maintenance practices. Unlike gasoline engines, diesel engines rely on compression ignition, making them more robust but also more sensitive to fuel, air, and coolant quality. These engines power vessels in various roles:
- Primary Propulsion: Used in yachts, motorboats, and commercial ships for main propulsion.
- Auxiliary Power (Gensets): Provide electricity for onboard systems, common in larger vessels or sailboats.
- Inboard vs. Outboard: Inboard engines are housed within the hull, often in a dedicated engine room, while outboard engines are mounted externally, offering easier access for maintenance.
Key Differences from Standard Diesel Engines
Marine diesel engines share core mechanics with other diesel systems but include unique features tailored to their environment:
- Fuel-Water Separators: These protect the fuel system from water contamination, critical in high-moisture marine settings.
- Raw and Freshwater Cooling Systems: Unlike air-cooled radiators in vehicles, marine engines use water-based cooling systems to manage heat, involving both seawater (raw water) and a closed freshwater loop.
The Importance of Cooling System Maintenance
The cooling system is the lifeline of a marine diesel engine, regulating temperature to prevent overheating, reduce wear, and maintain efficiency. A well-maintained cooling system offers several benefits:
- Enhanced Fuel Efficiency: Optimal temperatures ensure efficient combustion, reducing fuel consumption and costs.
- Reduced Engine Wear: Stable temperatures prevent excessive thermal expansion and friction, preserving engine components.
- Extended Service Life: Proper cooling minimizes thermal stress, prolonging the engine’s operational life.
Neglecting the cooling system can lead to severe consequences, such as corrosion, impeller failure, or catastrophic engine damage. Regular maintenance, as emphasized by 805 Marine Mechanic, is an investment in reliability and performance.
Key Components of the Cooling System
Understanding the cooling system’s components is essential for effective maintenance. Below are the primary parts and their roles:
- Raw Water Cooling System: Draws seawater to cool the engine’s freshwater loop. Key components include the sea strainer, raw water pump, and impeller.
- Freshwater Cooling System: A closed loop of coolant that absorbs heat from the engine’s internal components, regulated by a thermostat.
- Heat Exchanger: Transfers heat from the engine’s coolant to the raw water, expelling it overboard.
- Sacrificial Anodes: Protect metal components from corrosion by corroding preferentially.
- Thermostatic Valve: Regulates coolant flow to maintain stable engine temperatures (typically 70–90°C).
- Aftercooler, Lube Oil Cooler, and Transmission Cooler: Additional heat exchangers that cool specific systems, enhancing overall performance.
Diagram: Cooling System Flow
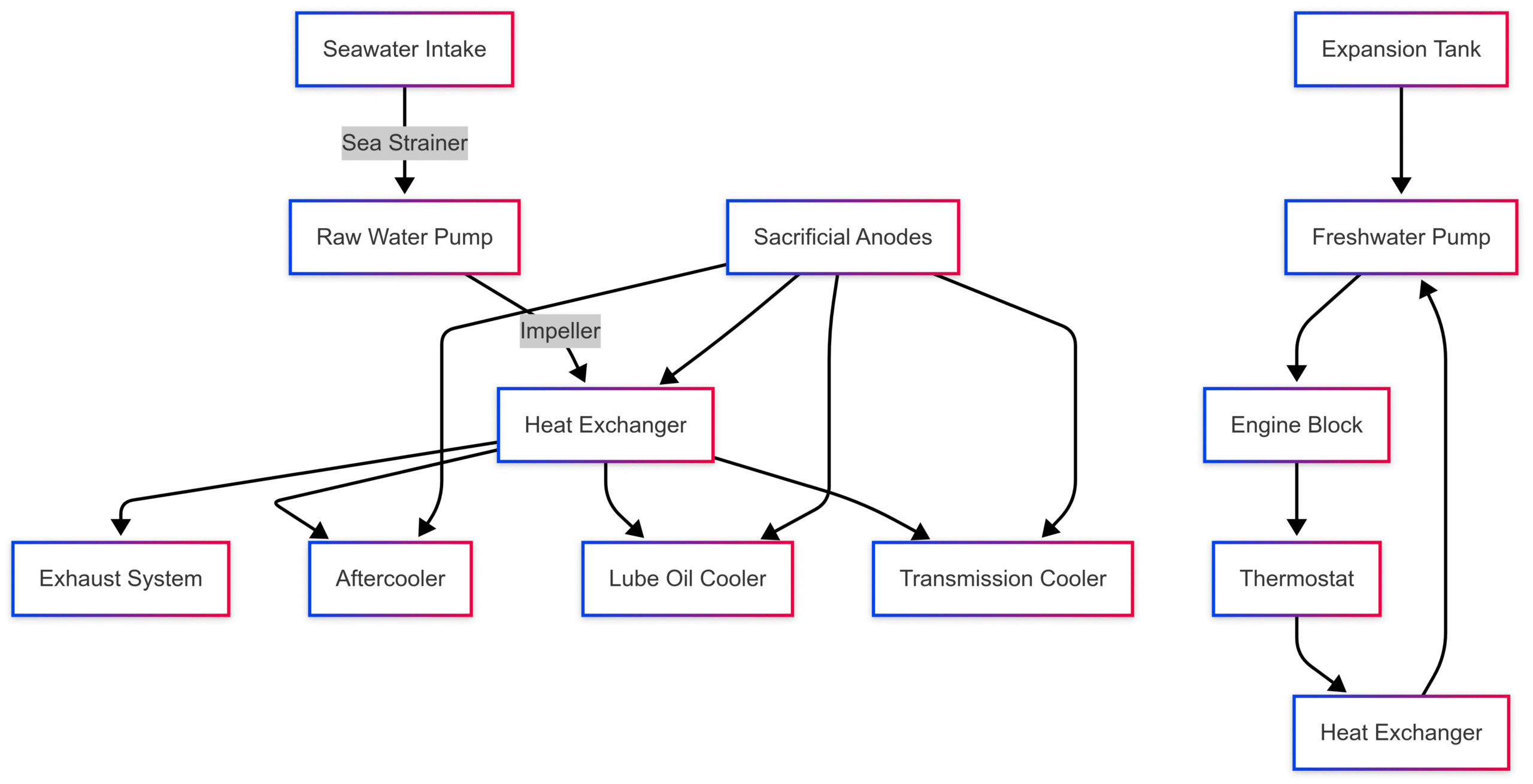
This diagram illustrates the flow of raw water and freshwater through the cooling system, highlighting the interaction between components.
Essential Maintenance Practices
Regular maintenance is crucial to prevent issues and extend engine life. Below are key practices for cooling system care and general engine maintenance, with specific guidance for MAN marine engines.
Cooling System Maintenance
Raw Water System:
- Sea Strainer: Clean regularly to remove debris and marine growth. Ensure the strainer lid is secure.
- Raw Water Pump and Impeller: Inspect the impeller for wear or damage. Replace annually or every 2000 hours, as it can burn out if run dry for over 30 seconds. Use neoprene impellers for durability in freshwater applications.
- Flushing: Flush the system with fresh water after each saltwater use to remove salt and debris. A freshwater flushing system, like those installed by 805 Marine Mechanic, simplifies this process. For example, a single quick-connect system can flush two main engines and a generator simultaneously.
- Descaling: Annually flush the raw water system with a descaling solution like Barnacle Buster to remove scale and marine growth. This can double the manufacturer’s recommended maintenance interval for heat exchanger servicing.
Freshwater System:
- Coolant Levels: Check at every fuel fill-up, using high-quality coolant (50-50 mix for -34°F protection). Test freeze point with a refractometer or test strip.
- Hoses and Clamps: Inspect for leaks or wear. Replace if damaged.
- Thermostat: Test every 2000–2500 hours by soaking in hot water (70–85°C) and measuring lift with calipers. Replace if it fails to operate within specs.
Heat Exchanger and Coolers:
- Clean annually during tune-ups using a descaling solution. Inspect for corrosion and replace sacrificial anodes (aluminum preferred over zinc for freshwater flushing systems).
- Check aftercooler, lube oil cooler, and transmission cooler for blockages or scale buildup.
Sacrificial Anodes:
- Inspect and replace every 6–12 months, depending on corrosion rate. Aluminum anodes are recommended for systems using freshwater flushing.
General Engine Maintenance
Beyond the cooling system, the following tasks ensure overall engine health:
- Oil and Filter Changes: Check oil levels and quality regularly. Normal oil is amber to black; milky, gritty, or diesel-smelling oil indicates contamination. Change oil and filters per manufacturer intervals (typically every 200–400 hours).
- Fuel System:
- Fuel Filters: Replace during oil changes to ensure clean fuel, critical for lubrication and combustion.
- Fuel-Water Separators: Inspect and drain water regularly.
- Fuel Conditioner: Add to prevent spoilage if the engine is unused for over a month.
- Air Filters: Replace regularly to ensure clean, oxygen-rich air for combustion.
- Belts: Check for cracks or brittleness. Adjust tension if deflection exceeds half an inch.
- Battery and Electrical: Inspect terminals for corrosion, ensure tight connections, and test battery voltage. Replace batteries over three years old.
- Exhaust System: Monitor for black (overloading), blue (oil burning), or white (water contamination) smoke, indicating potential issues.
WOBBLES Daily Checklist
The WOBBLES acronym simplifies pre-departure checks:
- Water: Check sea strainer, impeller, and coolant levels.
- Oil: Verify oil quality and levels in the crankcase and gearbox.
- Belts: Inspect for wear and proper tension.
- Battery: Ensure secure connections and adequate voltage.
- Leaks: Check for fluid leaks or corrosion.
- Exhaust: Confirm water flow and check for abnormal smoke.
- Sound: Listen for unusual noises.
- Spares: Keep spare impellers, filters, and belts onboard.
Comprehensive Inspection Checklist
For thorough maintenance, follow this checklist, tailored to MAN marine engines, with intervals based on manufacturer recommendations (e.g., every 1000 or 3200 hours):
Component | Inspection Task | Frequency |
---|---|---|
Engine and Fuel System | Check for leaks, rust, and fuel contamination | Every 200 hours |
Raw Water System | Clean sea strainer, inspect impeller | Monthly or 100 hours |
Freshwater System | Check coolant, hoses, and thermostat | Every fuel fill-up |
Heat Exchanger/Coolers | Flush with descaler, replace anodes | Annually or 1000 hours |
Battery/Electrical | Inspect connections, test voltage | Monthly |
Exhaust System | Monitor smoke and water flow | Every trip |
Drive Train | Inspect propeller, shaft, and anodes | Annually |
Record all maintenance in a log to track trends and schedule professional servicing.
Maintenance Schedule Example
A typical maintenance schedule for a MAN marine engine includes:
- Daily: WOBBLES checks before each trip.
- Monthly: Inspect fuel system, sea strainer, and battery.
- Every 200–400 Hours: Change oil, fuel, and air filters.
- Annually or 1000 Hours: Flush cooling system, clean heat exchanger, replace anodes.
- Every 2000–2500 Hours: Overhaul thermostatic valve, inspect major components.
Always consult your engine’s manual for specific intervals.
Real-World Benefits and Case Studies
Proper cooling system maintenance delivers tangible benefits, as illustrated by real-world examples:
- Case Study: Overheating Incident: A container ship in the South China Sea faced delays and $40,000 in repairs due to a stuck thermostatic valve, neglected beyond 3000 hours. Regular 2000-hour overhauls could have prevented this.
- 805 Marine Mechanic Success: A customer in Santa Barbara installed a freshwater flushing system, reducing maintenance frequency and extending cooling system life by minimizing salt corrosion.
Tools and Products for Maintenance
Product | Purpose | Approx. Price (USD) |
---|---|---|
Barnacle Buster | Descaling solution for raw water system | $20–$50 per gallon |
Neoprene Impeller | Raw water pump impeller | $30–$100 |
Aluminum Anodes | Corrosion protection | $10–$50 each |
High-Quality Coolant | Freshwater system coolant | $15–$40 per gallon |
Handheld Refractometer | Test coolant freeze point | $20–$100 |
Expert Tips from 805 Marine Mechanic
- Freshwater Flushing System: Install a system for easy post-trip flushing, reducing salt buildup and maintenance frequency.
- Professional Servicing: For complex tasks like thermostatic valve overhauls, rely on certified mechanics like 805 Marine Mechanic for precision and reliability.
- Aluminum Anodes: Prefer aluminum over zinc for systems with freshwater flushing, as they corrode more effectively.
Conclusion
Maintaining the cooling system of your MAN marine diesel engine is a proactive investment in performance, efficiency, and longevity. By understanding key components, following a rigorous maintenance schedule, and leveraging tools like freshwater flushing systems and descaling solutions, you can prevent costly breakdowns and ensure smooth sailing. With expert guidance from 805 Marine Mechanic, boat owners in Ventura, the Channel Islands, and Santa Barbara can transform their maintenance approach, safeguarding their vessels for years of reliable service. Regular checks, detailed record-keeping, and adherence to manufacturer recommendations are your best tools for unleashing peak performance on the open waters.
Happy Boating!
Share Marine Diesel Engine Maintenance And Cooling Systems with your friends and leave a comment below with your thoughts.
Read How to Check Performance Data in Marine Diesel Engines until we meet in the next article.